A woven wire mesh, also known as a woven wire cloth, is made by weaving wire strands in an overunder method or underover method to form different patterns with varying specifications. Some of the most common weave patterns are explained below.
Mesh weave pattern has a significant impact on which use cases it is suitable for. In general, square weaves are well suited for general-purpose applications, while dutch weaves are better suited for air and water filtration.
The size and material of woven wire mesh vary in addition to the weave. Various opening sizes are available, from just a few microns to several inches, as well as metals including aluminium, brass, copper and mild steel.
We hope that this page explains woven mesh for you. This image shows a standard plain stainless steel woven wire mesh panel.
Let’s go…
What Is The Difference Between Woven Wire Mesh & Welded Wire Mesh?
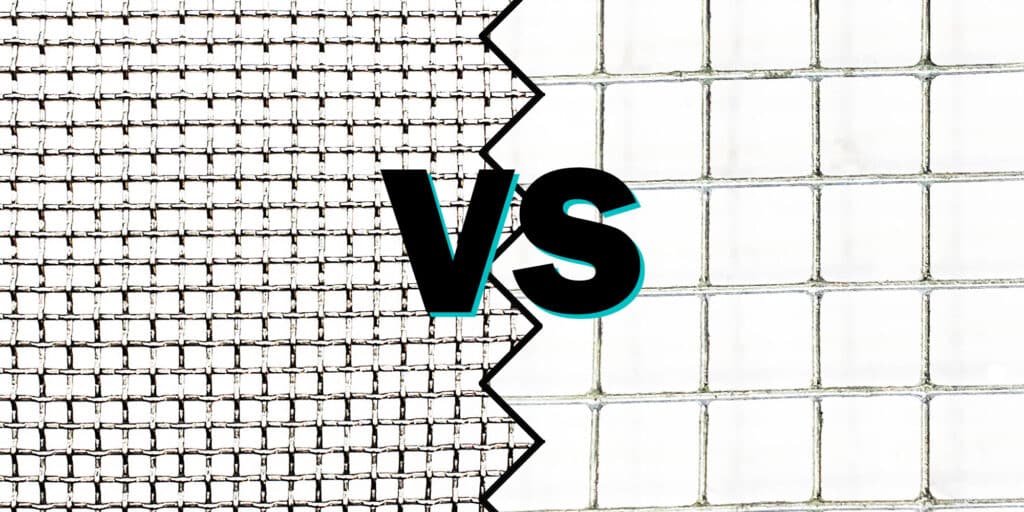
As the name suggests, The Mesh Company are specialists in all things wire mesh. Our group of companies has been a major supplier of woven and welded wire mesh since 1878. The oldest version of our company brochure makes for an interesting read.
Various types of wire mesh are possible, including woven and welded versions, all of which offer unique advantages suitable for myriad industrial applications.
But what is the difference between woven and welded?
In the woven wire mesh industry, a wide variety of mesh types can be manufactured from fine woven meshes for use in micronic filtering applications all the way to coarse woven meshes for use in fencing and security screens.
A key advantage of the material is that it is also more flexible, making it ideal for use with parts and products that have irregular or unusual contours and shapes. Woven mesh can be as fine as silk or cloth because of the fineness of the wires used to weave the mesh, which is far finer than that used to weld the mesh.
Simply put, by weaving mesh on a loom it is possible to go much finer and give a much larger range of size options. For example, this mesh has 500 wires per linear inch.
Welded wire mesh is stronger and more rigid than woven wire mesh, making it suitable for use as a protective or barrier material. Due to the welded wire strands, this type of mesh is suitable for parts and products that require tight dimensional tolerances. This rigidity makes welded mesh ideal for fencing.
We recently wrote a detailed article discussing this mesh matchup. If you require a deeper dive into this subject then we suggest that you check it out.
Benefits Of Choosing Woven Wire Mesh
A number of advantages are provided by woven wire mesh when used in industrial and commercial applications, such as:
- Huge range of options due to the limitless possibilities given by the weaving process. As an example, our standard woven stainless steel mesh ranges from 11.1mm hole all the way down to 0.26mm hole. This illustrates the multitudinous range of options that are are available to our customers.
- Despite being subjected to shock, impact, and other stresses, woven wire mesh retains its structural integrity due to its interwoven and clinched construction.
- The manufacture of woven wire mesh has been optimised by many manufacturers to reduce waste and increase productivity, which results in lower prices for customers. This is especially true for our group as we have so many years of experience in the production of this product.
- A woven wire mesh provides better visibility, circulation, ventilation, and acoustics within a building due to the numerous openings that permit light, air, and sound to pass through relatively unobstructed.
- The simplicity of cleaning and maintaining woven wire mesh results in a reduction in labour costs and time spent on such operations.
- There is a wide range of patterns, materials, and sizes available in woven wire mesh, as indicated above. It is true that many manufacturers offer an extensive selection of standard options, but some manufacturers also offer custom solutions to meet the needs of customers with highly specific or unique requirements.
Popular Applications For Woven Wire Mesh
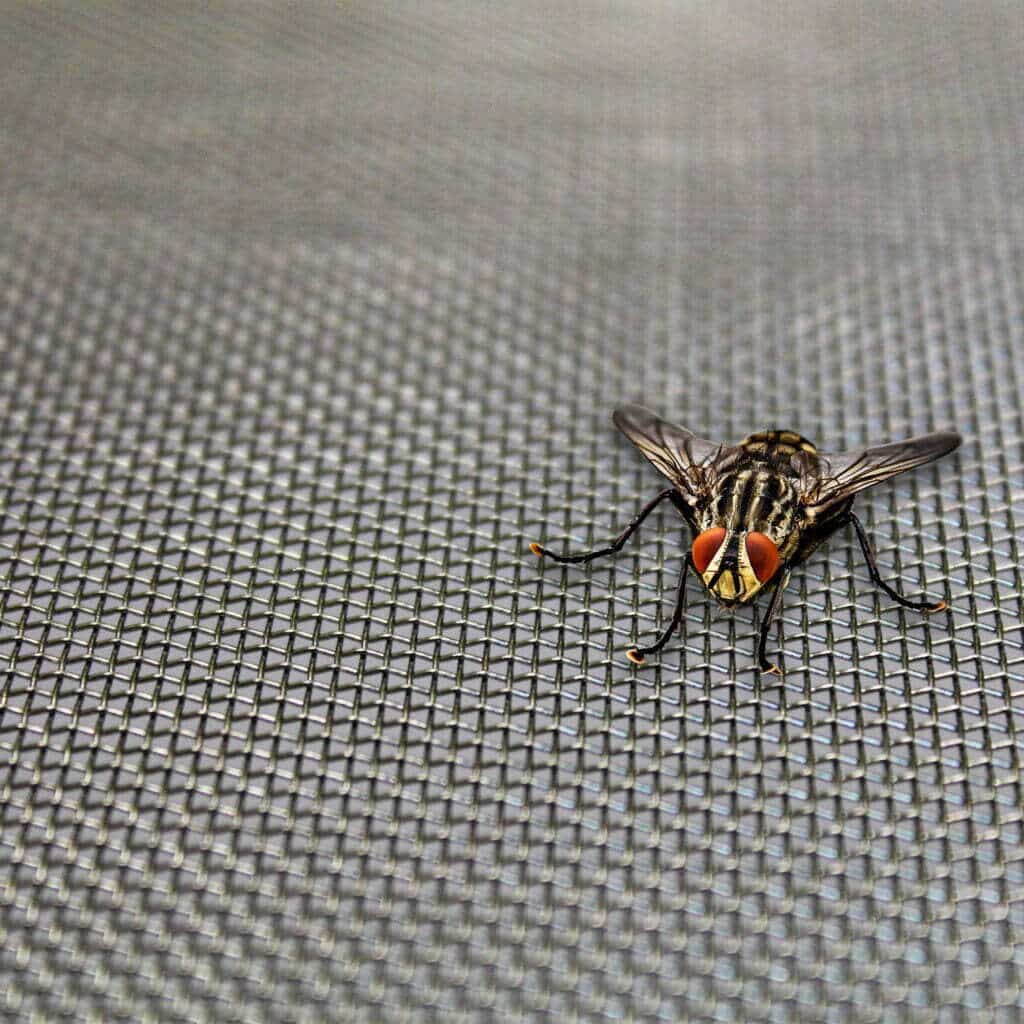
- RMI & EMI Shielding Woven wire mesh is effective in shielding against Radio Frequency Interference (RFI) and Electromagnetic Interference (EMI), commonly used in electronic enclosures to prevent signal disruption.
- Rodent Deterrent The strength and durability of wire mesh make it an ideal barrier against rodents, preventing them from accessing and damaging property.
- Insect Mesh Finely woven wire mesh serves as an excellent barrier against insects, providing ventilation while keeping bugs out.
- Filter Mesh Wire mesh is used in filtration systems due to its precise weave patterns and varied aperture sizes, suitable for both liquid and air filtration.
- Baskets Crafted into baskets, wire mesh offers ventilation and durability, ideal for industrial and domestic use.
- Fencing Woven wire mesh provides secure and durable fencing solutions for various applications, including agricultural, industrial, and residential.
- Filtering and Separating Components It plays a crucial role in the separation and filtering processes in various industries, including chemical, food, and pharmaceutical.
- Grates and Grills Used in grates and grills, wire mesh offers heat resistance and strength, suitable for cooking and industrial applications.
- Safety Handrails and Guardrails Wire mesh adds a protective and aesthetic element to handrails and guardrails, ensuring safety without obstructing views.
- Screens for Medical Centrifuges In medical centrifuges, wire mesh screens are used for their precision and durability.
- Racking Ideal for storage and display, wire mesh racks are robust and provide excellent visibility of items.
- Inspecting Screens In quality control processes, inspecting screens made of wire mesh are used for their accuracy and reliability.
- Stands and Shelving Wire mesh is also utilized in making stands and shelving, offering strength and a modern aesthetic.
What Weave Types Are There?
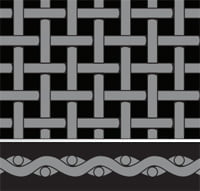
Plain weave woven wire mesh is used for the majority of wire mesh woven by The Mesh Company. Each warp wire crosses alternately above and below every weft wire and vice versa. Warp and weft wires are normally of the same diameter. This weave type is used for the majority of commercial applications and for filtration where a high flow rate is required.
Throughout the fabric, weft wires alternate above and below successive pairs of warp wires. It is possible to use a heavier wire diameter in this weave than in a plain weave wire mesh with the same mesh count.
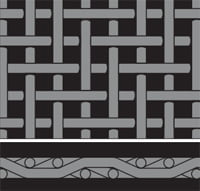
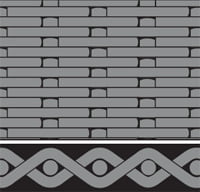
Twill Dutch Weave
In contrast to Plain Dutch Weave, there is a double layer of weft wires that are woven in a twill pattern. In addition to being “light tight”, this wire mesh has a very smooth surface and is extremely strong, but it has a limited flow rate. Often used in critical filtration applications under high pressure, this wire cloth is also known as Micromesh wire cloth.
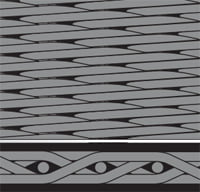
How Is Woven Mesh Made?
Weaving plain woven wire mesh is similar to traditional textile weaving. A grid-like structure is formed by interlacing individual wires. Wire material is selected first, which can vary depending on the desired mesh properties, such as strength, flexibility, or corrosion resistance.
The weaving process involves setting up the warp wires – the long wires that run the length of the mesh. These are held taut and in place on the loom. The weft wires are then interwoven through the warp wires, alternating over and under each warp wire. This process is repeated, with each weft wire lying parallel to the others, and perpendicular to the warp wires.
Using precision machinery, the mesh is uniform in spacing and wire diameter. Modern looms used for this process can be highly automated, allowing for efficient production of large quantities of wire mesh with uniform quality. It can be used in a variety of applications, from industrial filtration to home décor.
What Is The Best Method For Cutting Wire Mesh?
We would recommend a range of cutting tools based on the thickness of the wire that we used to weave our various meshes.
Simply take the cutting tool required for the job and cut along the line of the aperture. Cutting across the wires will leave sharp edges and may reduce the structural integrity of the weave.
We would suggest:
-
- Using an angle grinder or guillotine to cut 11.1mm hole and 6.87mm hole mesh. Both of these mesh specifications are strong and not at all easy to cut.
- We would use tin snips to cut every other mesh size in our heavy duty section.
- Every mesh size in our coarse section should be cut with standard kitchen scissors.
Anything with smaller holes than that should be cut by hand, as you would with a fine fabric. We would use that method of cutting for every size in our fine and super-fine sections.
Our YouTube channel shows various means of cutting our mesh materials. Check us out there for more information.
Again, if you would rather we cut your mesh to size for you then please contact us with your requirement.
The Mesh Company: Woven Wire Mesh Specialists
The experts at The Mesh Company will happily assist you with all of your wire mesh requirements. In addition to manufacturing and distributing wire mesh, woven wire cloth, and welded mesh, we serve a wide range of industries, including aerospace, agriculture, automobile, construction, pharmaceuticals and many others.
And we stock a lot more than just stainless steel woven mesh and welded products. Through our site we offer a variety of metals including aluminium, brass, copper and mild steel in many hole sizes and thicknesses.
We would be delighted to assist you with any upcoming wire mesh application or provide more information about our products and services. Please get in touch with our friendly team if you have any questions or concerns regarding wire mesh.
As always, thank you for checking out our blog. We hope that this helps you with your project. We try to launch a couple of new guides every week. Eventually we will have covered everything there is to cover about mesh.
You may be interested in our blog that explores woven wire vs welded wire mesh.
Our goal for our blogs and help guides is to answer as many questions as possible to help to explain the possibilities of mesh to our customers.
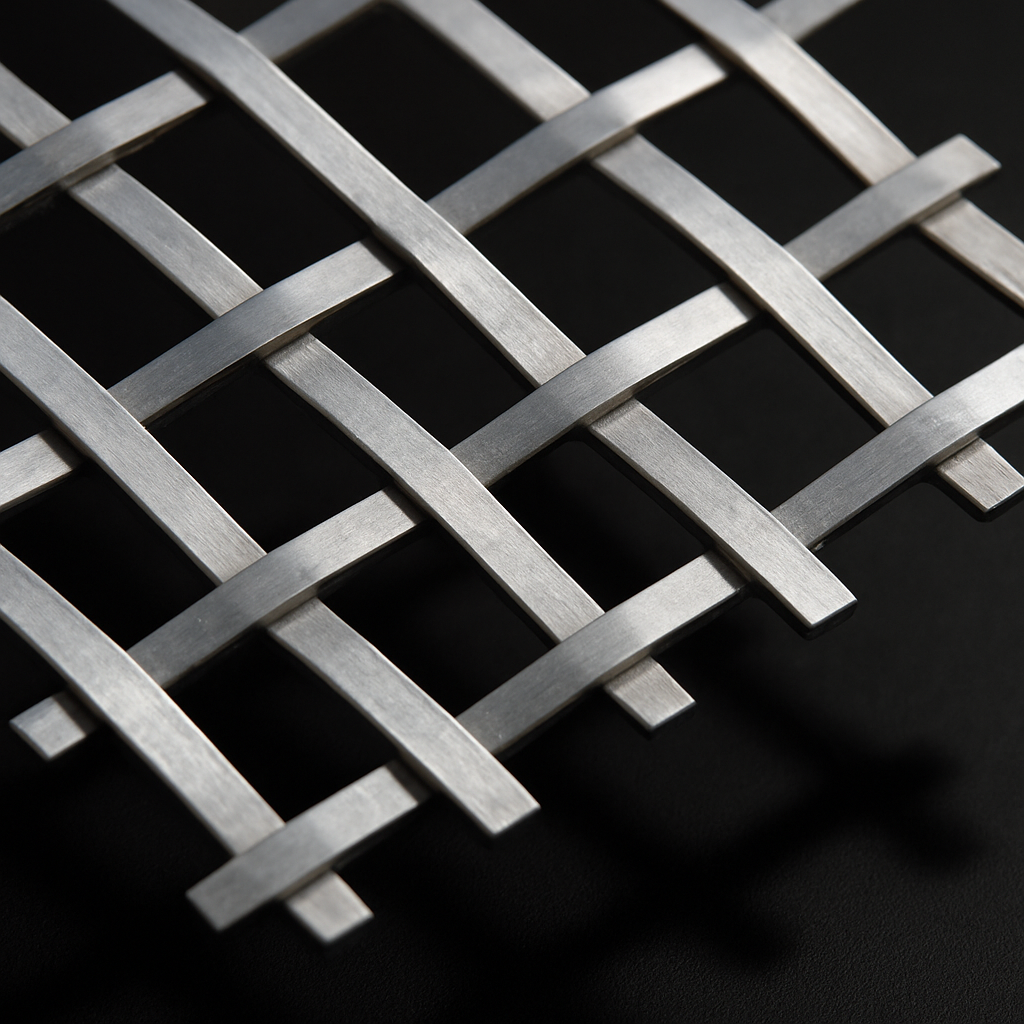
What Is Lattice Mesh and Why Choose Stainless Steel 304?

Introducing Our Brass-Coloured Aluminium Lattice Weave Mesh: Style Meets Practicality
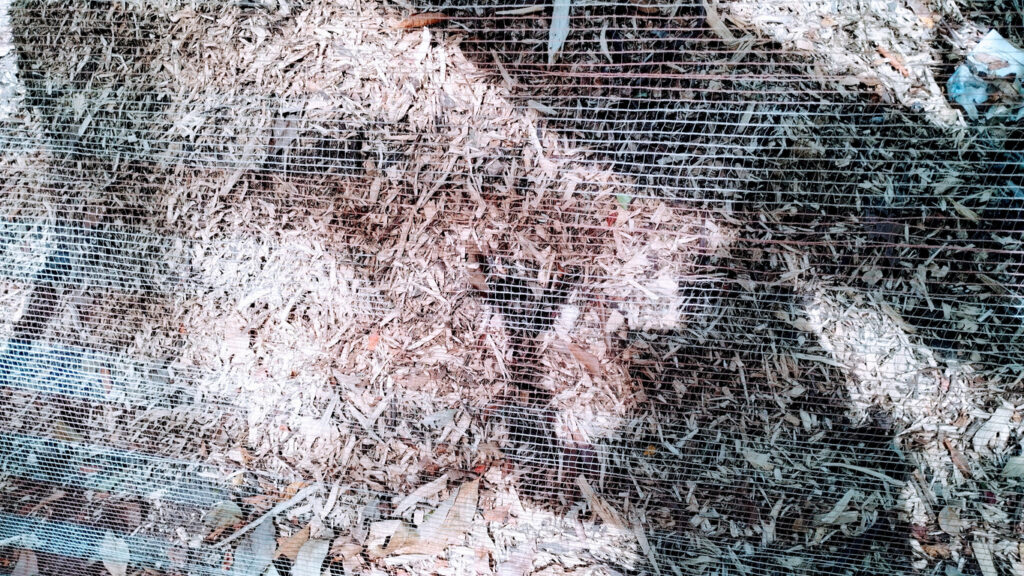
How Vent Mesh Protects Against Rodents and Debris
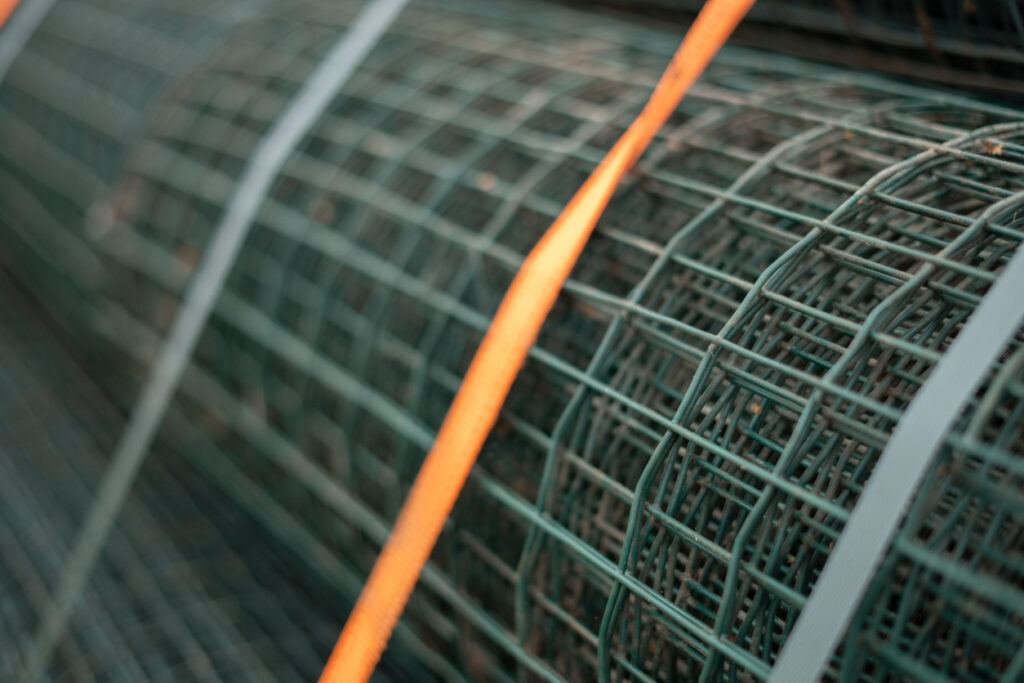
Benefits of PVC-Coated Galvanised Steel Fencing: Strong, Stylish, Long-Lasting
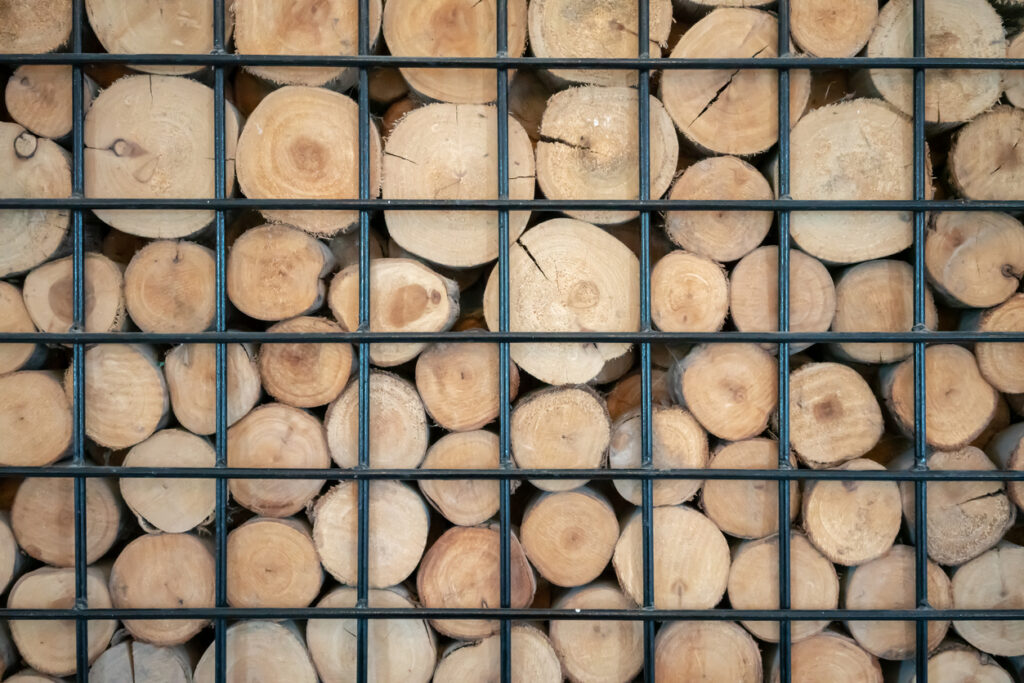
Firewood Mesh: Keeping Your Logs Dry and Secure
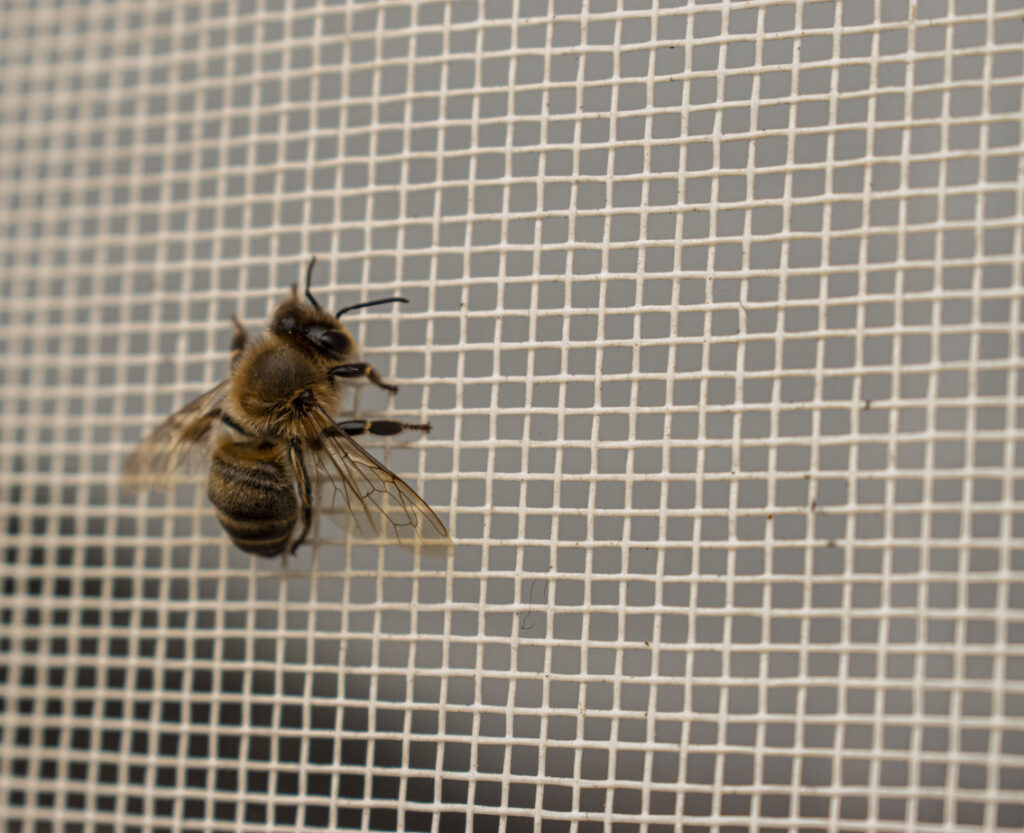
Hive Mesh for Beekeeping: Safer Hives with Stainless Steel Mesh
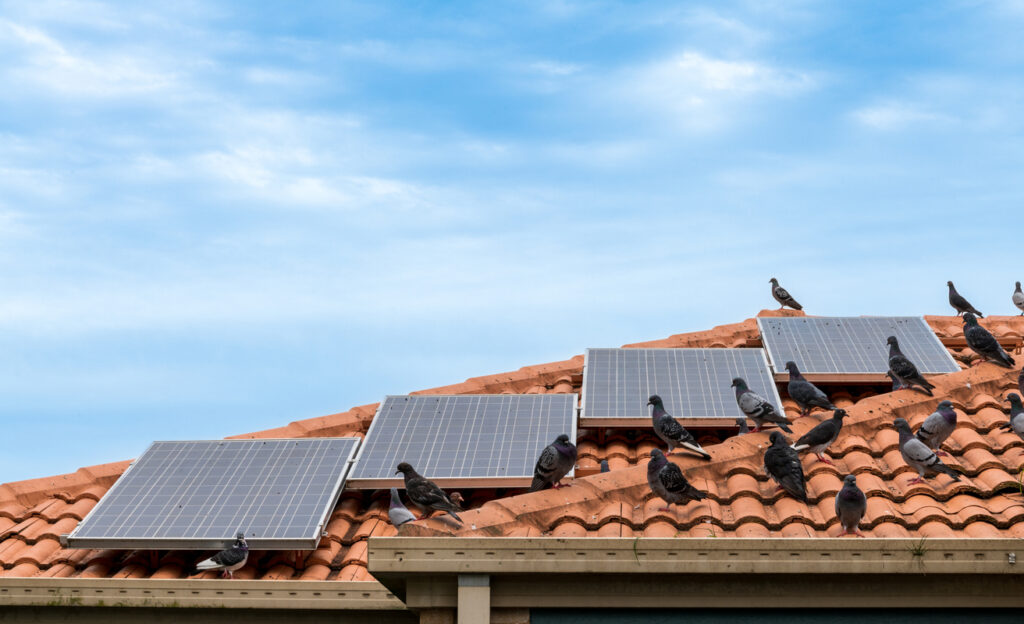
How To Use Solar Panel Mesh to Stop Birds Nesting Underneath
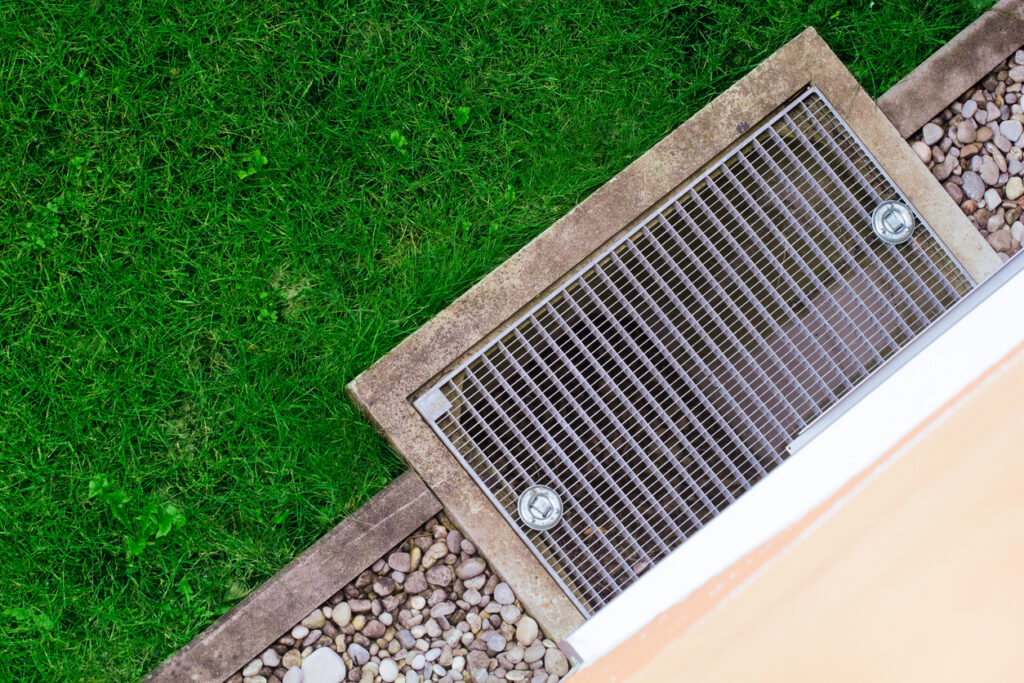
Choose the right stainless steel mesh for outdoor drainage.
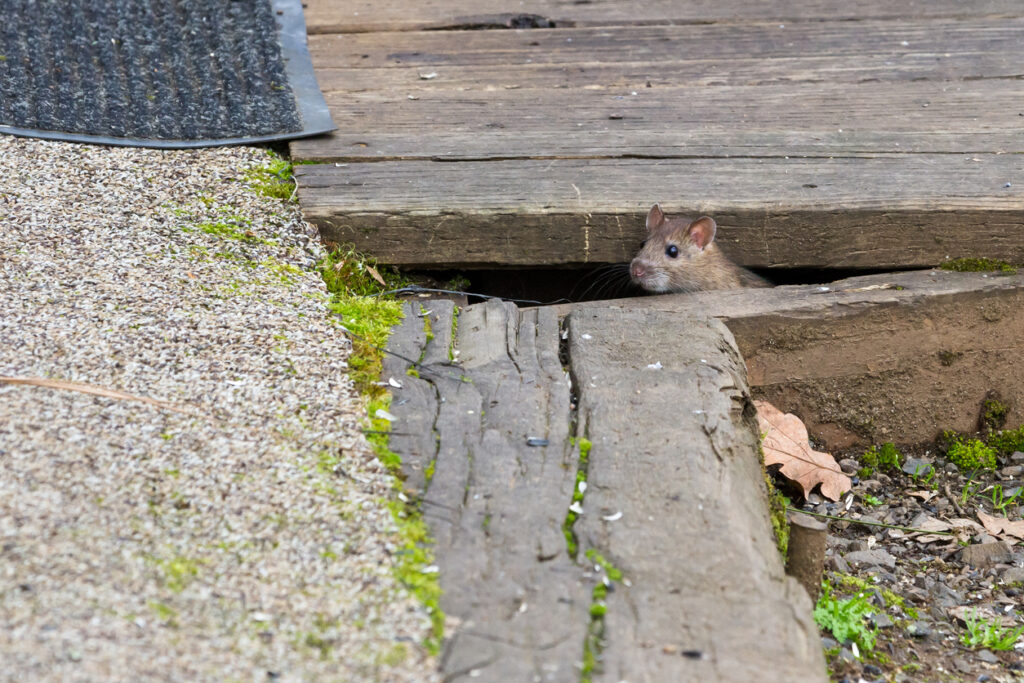