Stainless steel stands as a hallmark of durability and versatility in the realm of perforated metal mesh manufacturing, championing a broad spectrum of industrial, architectural, and design applications.
With its inherent corrosion resistance, strength, and sleek aesthetic, stainless steel is the ideal material for precision perforation. Round or square holes represent more than just an aesthetic choice; they influence the mesh’s performance, application suitability, and visual appeal.
Comparing round versus square-hole stainless steel perforated mesh sheds light on the respective advantages, applications, and nuanced considerations that dictate their selection.
To provide a comprehensive understanding of how each hole type impacts the mesh’s utility and aesthetic contribution to projects, we aim to explore a range of sizes – from the finer 0.75mm round holes with a 1.5mm pitch to the larger 20mm round apertures – and compare them with square hole alternatives. As a result of this examination, an informed decision can be made, ensuring the chosen perforated mesh aligns with the specific performance requirements and design aspirations.
The Basics of Perforated Metal Mesh
Perforated metal mesh is created by punching holes into stainless steel sheets, a process that can be accomplished by mechanical means or laser cutting. The method not only defines the mesh’s structural characteristics, but also its aesthetics and functionality. The popularity of stainless steel for perforation can be attributed to its corrosion resistance, structural integrity, and modern, clean appearance. Despite its visual appeal, the mesh is able to withstand demanding environments.
A mesh’s functionality is determined by the hole shape and size. Airflow, light penetration, and material strength are directly affected by the open area ratio. With a higher open area ratio, round holes facilitate better airflow, making them ideal for applications requiring efficient ventilation. For applications requiring structural integrity, square holes may provide a more uniform distribution of strength across the mesh.
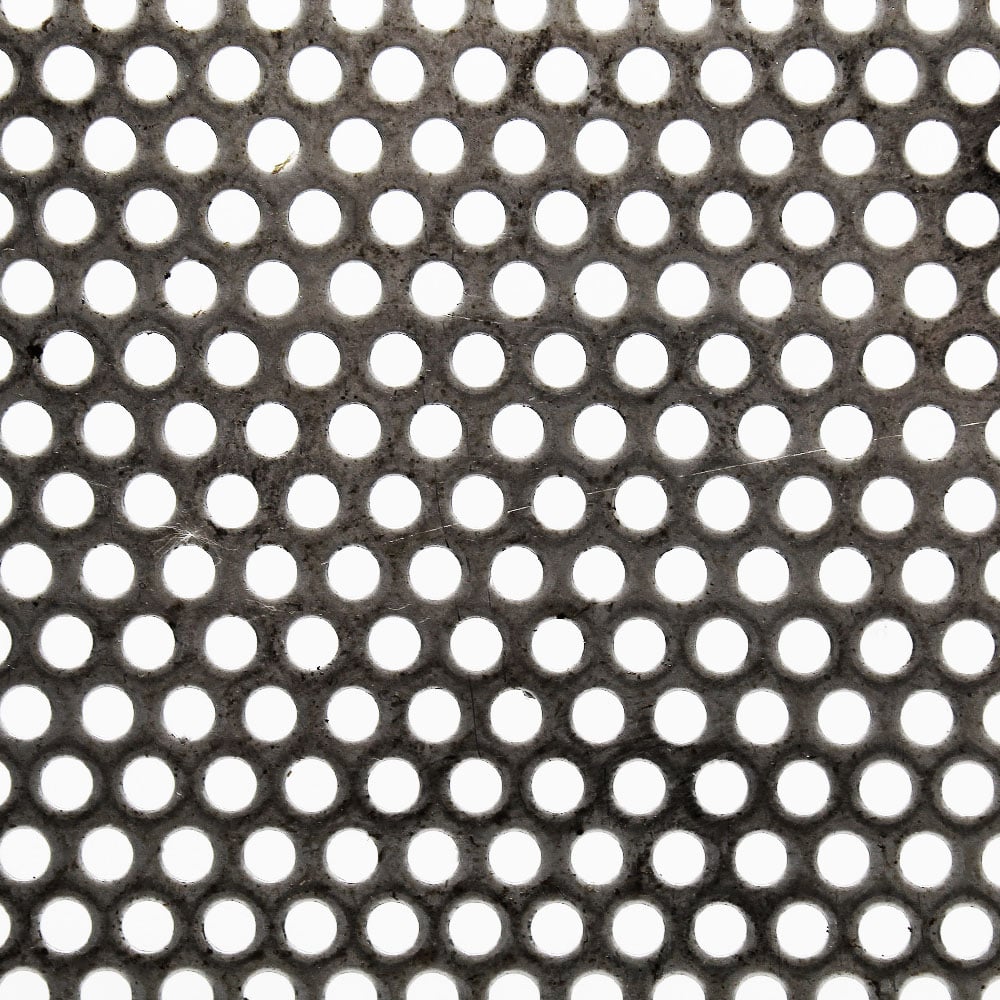
Round Hole Perforated Stainless Steel Mesh
Stainless steel mesh with round holes is known for its versatility and aesthetic uniformity. A 0.75mm hole with a 1.5mm pitch, for example, offers precision filtration capabilities suitable for pharmaceuticals and food and beverage applications. In architectural applications, such as facades and decorative panels, larger holes, such as 15mm with a 21mm pitch, contribute to a building’s visual identity while providing functional benefits, such as light filtration and air circulation.
In addition to their functional appeal, round holes also provide a visually harmonious solution, enhancing the mesh’s consistency and orderliness. Applications where the mesh is a prominent design element, such as architectural facades or interior partitions, benefit greatly from this aesthetic quality.
Round hole mesh should, however, be selected based on specific project requirements. Despite the high open area ratio of round holes, they may not always provide the strength necessary for certain structural applications. The uniform distribution of material around each hole makes round perforations less efficient than square holes, which might affect the choice of material for large-scale projects.
Stainless steel mesh with round holes has a wide range of applications, from enhancing building aesthetics to improving industrial processes.
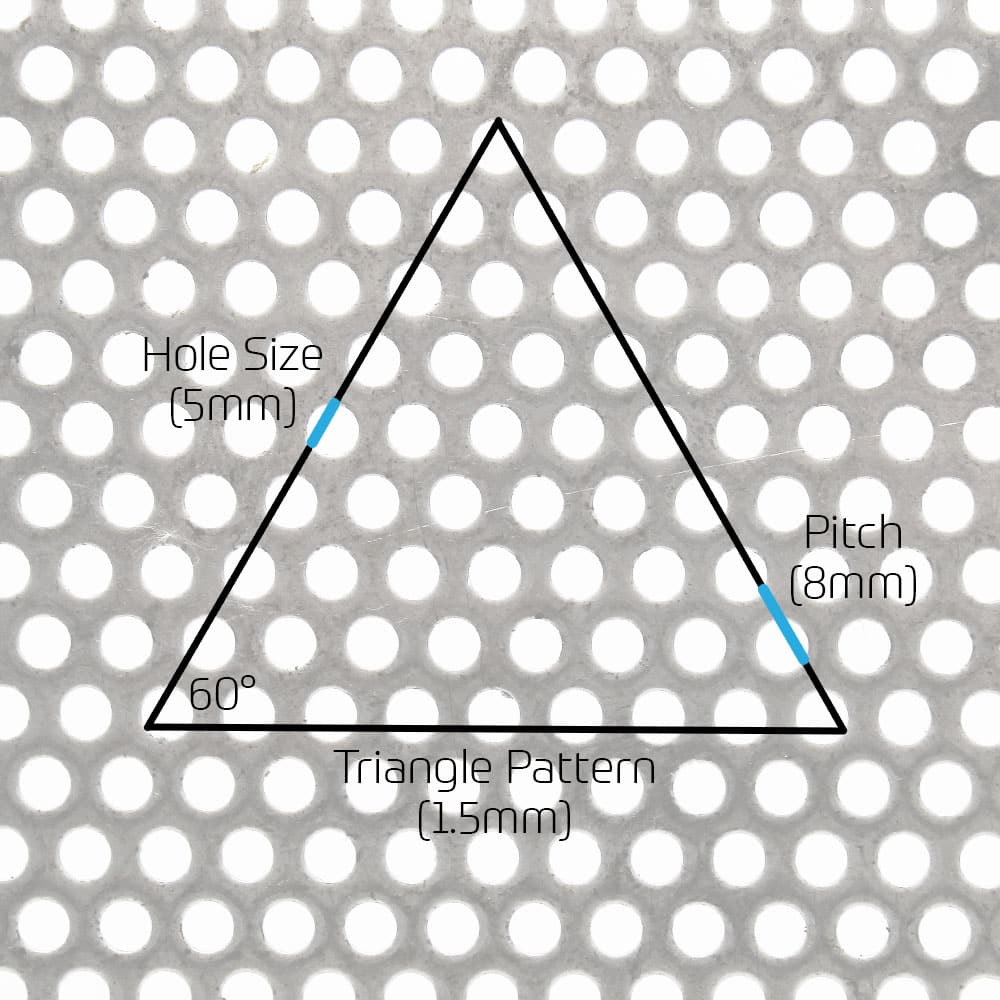
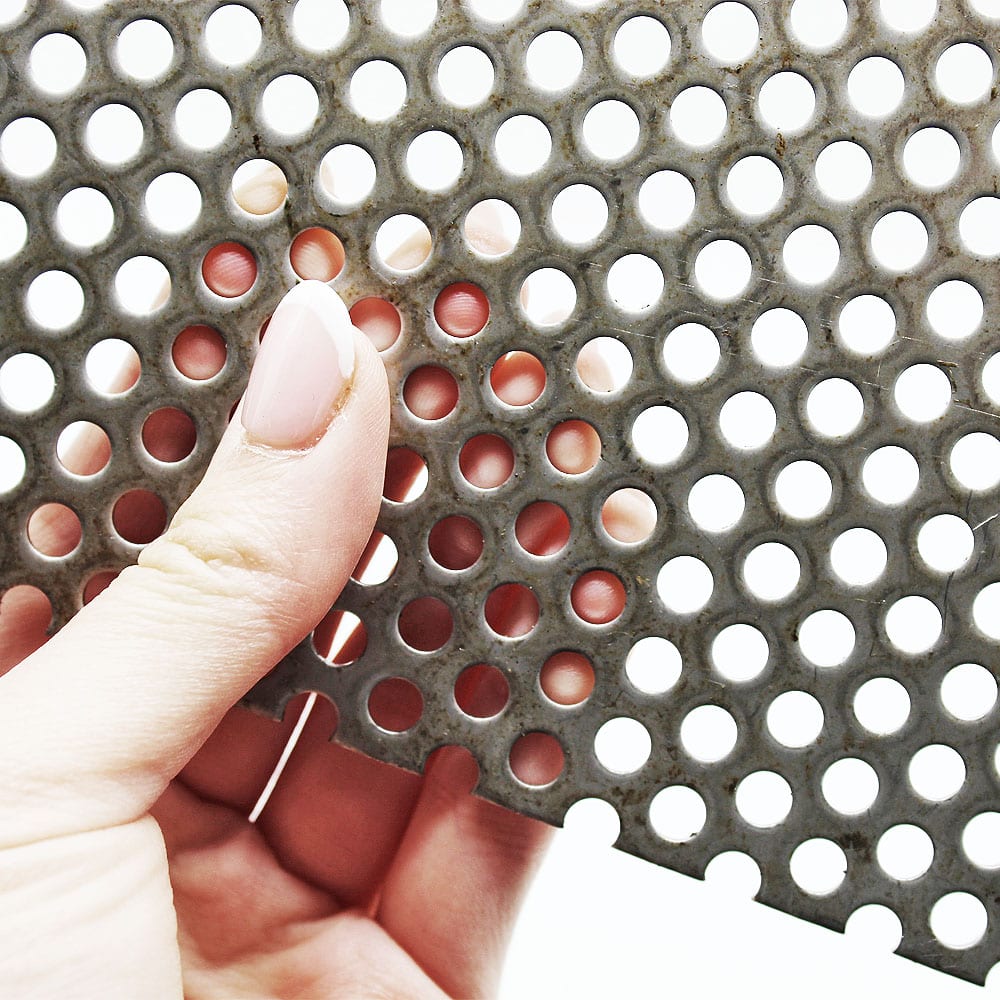
Square Hole Perforated Stainless Steel Mesh
Stainless steel perforated mesh with square holes, such as the 5mm square hole with an 8mm pitch and the 10mm square hole with a 12mm pitch, offers distinct benefits and applications. A major advantage of square holes is their uniform strength distribution across the mesh. Unlike round holes, which can concentrate material around the perimeter of each circle, square holes distribute metal evenly between adjacent holes. In applications where the mesh is subject to uniform loads or stresses, this can provide enhanced structural integrity.
A square hole can also have a larger open area than a round hole of similar size. This feature is particularly advantageous in filtration and screening applications where maximizing flow rate without sacrificing particle retention is crucial. Using square holes allows for closer spacing between holes, thereby expanding the mesh’s open area and, consequently, allowing more material to pass through in a given period.
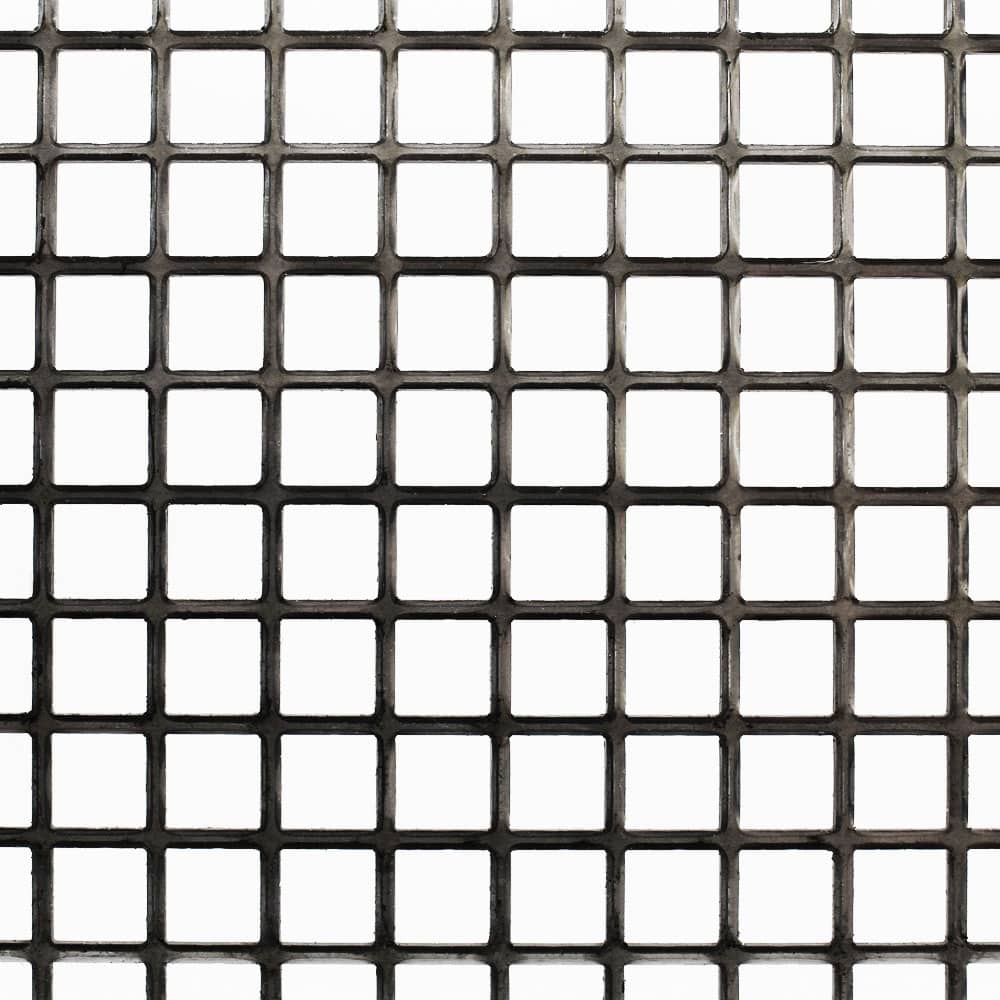
Square hole mesh can be used in architectural design to create visually striking patterns that play with light and shadow. Square holes’ geometric precision lends them a modern and orderly aesthetic, making them a popular choice for facades, cladding, and decorative panels. Furthermore, square holes can be appealing in designs that emphasize regularity and uniformity.
Additionally, square hole mesh is used in mechanical settings where precise particle retention is necessary. Square hole mesh is an ideal choice for sieves, grilles, and filters in the automotive, chemical, and food processing industries due to its sharp edges and uniform dimensions.
Square hole mesh does have its own challenges and considerations, however. In comparison with round hole mesh, square hole mesh can be more complex to manufacture, potentially leading to higher costs. In addition, square holes may collect debris or become stress concentration points, affecting the mesh’s longevity and maintenance requirements due to their sharp corners.
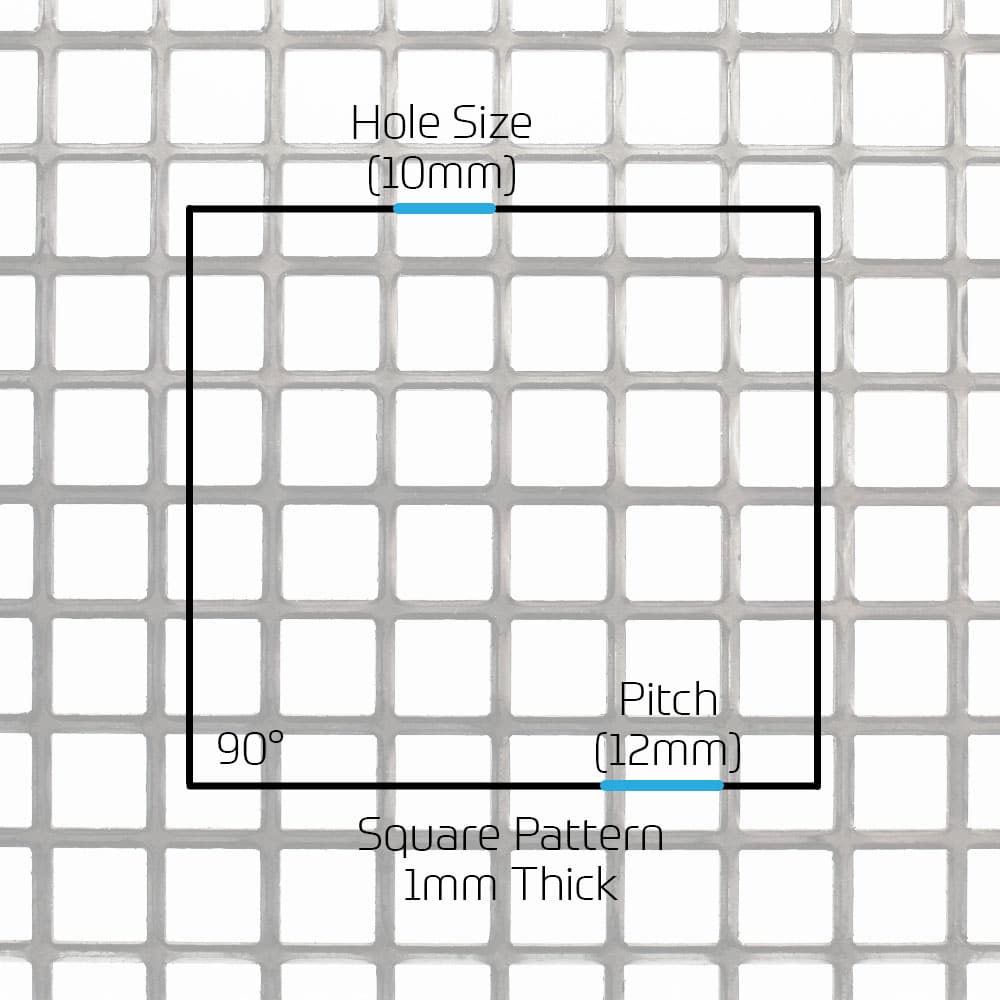
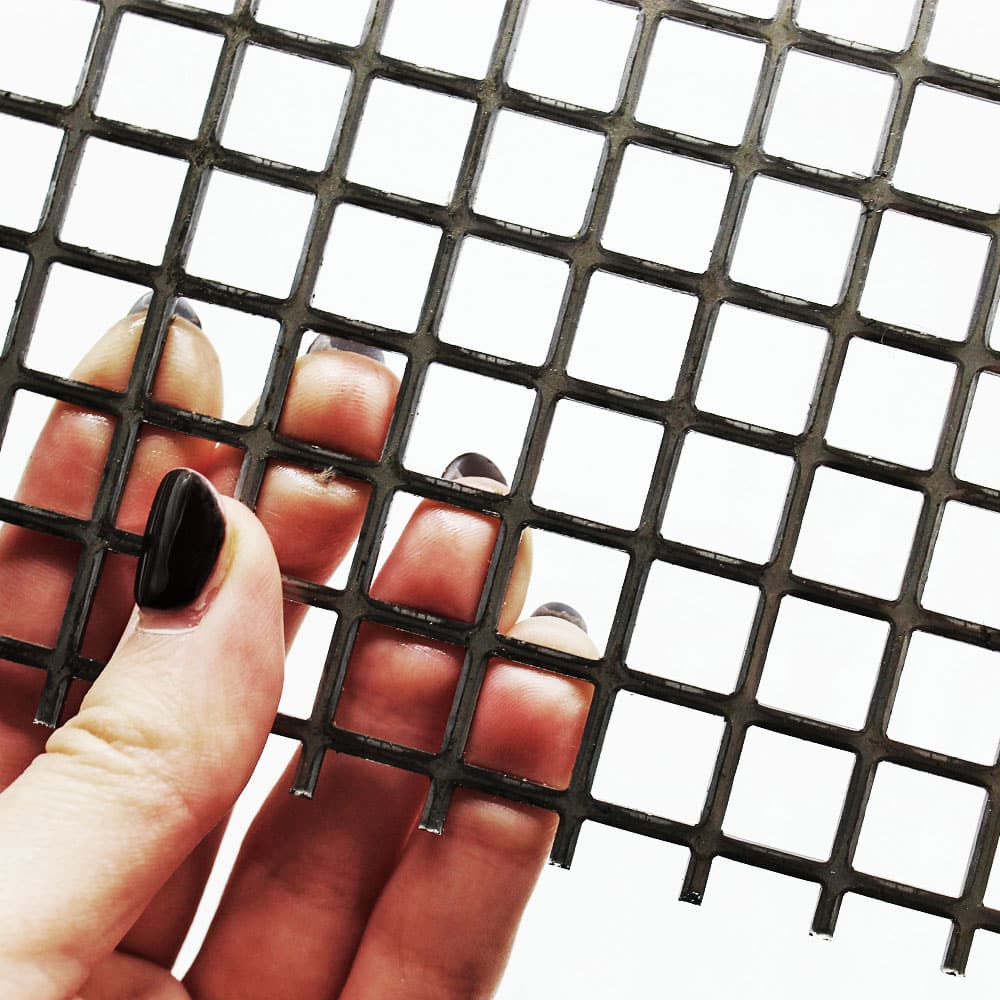
Comparative Analysis and Selection Criteria
Several factors play a critical role in the decision-making process when comparing round and square hole stainless steel perforated mesh. Square holes provide a more uniform strength distribution, while round holes are better suited to applications where stress is not uniform.
Additionally, aesthetics play a significant role; round holes offer a more traditional appearance, which may be preferred in certain architectural contexts, while square holes are more modern and geometric in nature.
In applications requiring efficient ventilation, such as HVAC systems and radiator covers, round holes typically allow for greater airflow. With their higher open area, square holes are better suited for applications requiring maximum material flow, such as industrial filtration and screening.
For large-scale projects, material efficiency is also an important criterion, with square holes providing a greater surface area per unit of material used.
Choosing the right hole shape for a particular project requires balancing these considerations against the project’s unique requirements. Generally, industries focusing on aesthetic architectural applications prefer square holes, whereas projects requiring optimal airflow might benefit more from round holes.
Stainless steel perforated meshes with round and square holes offer distinct advantages that make them suitable for a wide range of applications. Consider factors such as structural requirements, aesthetic goals, and functional efficiency when choosing between them.
We hope that this investigation of the nuanced differences between round and square hole stainless steel perforated mesh has revealed a wealth of factors that influence their selection for various applications.
In addition to purely aesthetic considerations, this comparative analysis highlights the critical importance of structural integrity, functionality, and aesthetic appeal when choosing between round and square perforations.
Round and square hole meshes benefit from stainless steel’s inherent properties of durability, corrosion resistance, and visual appeal. However, it’s often the specific requirements of the application that determine which hole shape is most suitable. With their ability to facilitate superior airflow and filtration efficiency, round holes are ideal for applications requiring ventilation or particle separation. Square holes, which offer a higher open area and uniform strength distribution, are preferred in situations where structural integrity and maximum throughput are paramount.
Choosing between these two options requires a careful evaluation of the project needs. The performance requirements, such as load-bearing capacity and filtration precision, the environment that may affect durability, as well as aesthetic preferences determine the mesh’s visual impact, all play a significant role in this decision-making process. To select the right mesh, a unique set of criteria must be considered for each project.
This analysis highlights the need for a tailored approach to selecting perforated mesh. The stakeholders should consider how each aspect of their project-from performance to aesthetics-will influence the overall success of the application.
Choosing between round and square hole stainless steel perforated mesh requires a thorough understanding of both the material’s properties and the application’s requirements. Perforated mesh specialists can provide expert guidance and insights that are invaluable.
It is important to consult with specialists and consider practical examples from similar industries to ensure the selected mesh meets all requirements for successful application.
As always, thank you for checking out our blog. We hope that this helps you with your project. We try to launch a couple of new guides every week. Eventually we will have covered everything there is to cover about mesh.
You may be interested in our blog that explores using stainless steel perforated mesh for ventilation.
Our goal for our blogs and help guides is to answer as many questions as possible to help to explain the possibilities of mesh to our customers.