When embarking on a project that involves filtration, separation, or protection, selecting the right type of wire mesh is crucial. Among the various weaving styles available, twill and reverse twill wire mesh are prominent choices due to their unique properties and functionalities.
This blog will delve into the distinctions between twill vs reverse twill wire mesh, helping you decide which mesh is best suited for your specific needs.
Understanding the Basics: What is Twill and Reverse Twill Wire Mesh?
Firstly, let us define what the terms “twill” and “reverse twill” are before we go into the differences and applications of both of these terms.
The term wire mesh refers to a fabric made from interwoven wires that can be used in a multitude of industrial, commercial, and residential applications, due to its versatility and versatility. As a result of how these wires are interwoven, there is an impact on the strength, flexibility, and suitability of the mesh for a variety of different applications.
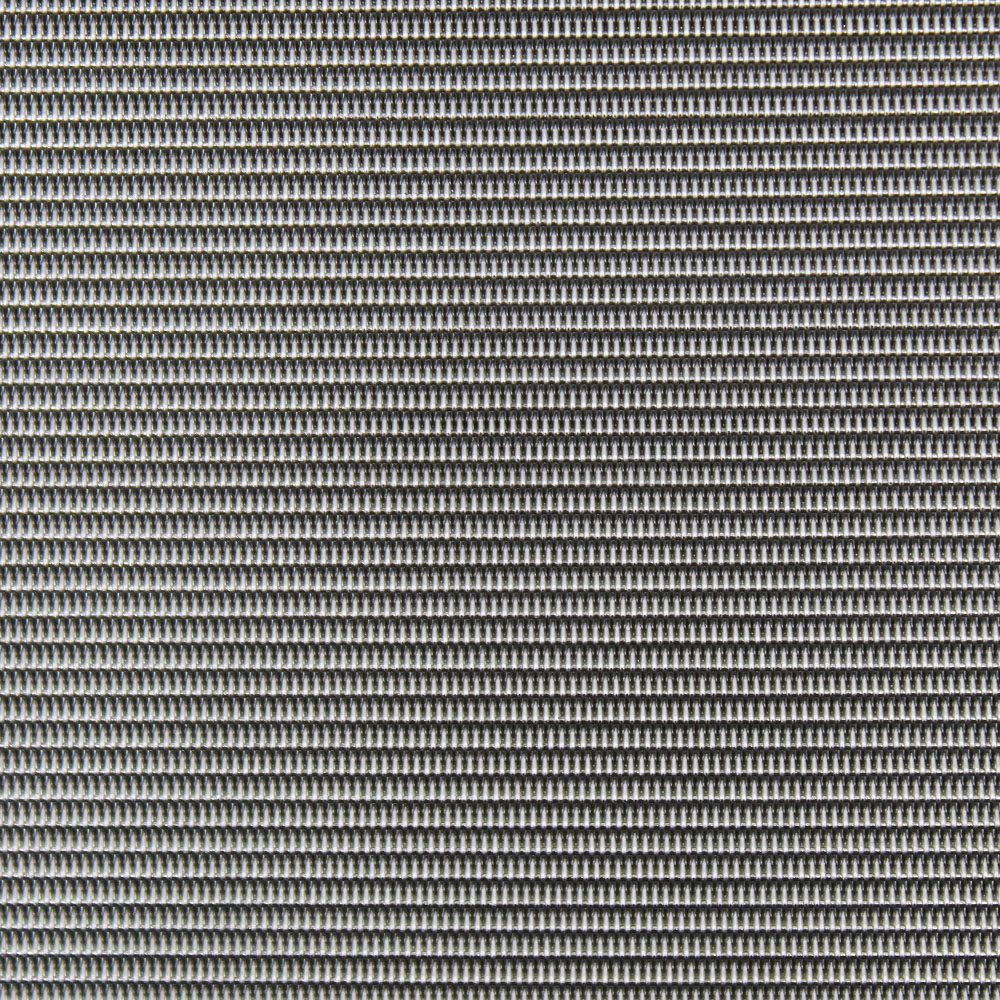
Twill Wire Mesh
Twill woven wire mesh is distinguished by its unique weaving pattern, where each wire in both the weft (horizontal) and warp (vertical) directions alternates by passing over two and then under two successive wires. This creates a distinctive diagonal pattern, giving the mesh its characteristic look and enhanced mechanical properties.
The twill weave pattern results in a mesh that is denser and more robust compared to the plain weave. This increased density provides higher strength and durability, allowing the mesh to handle heavier loads and withstand more rigorous conditions without losing its structural integrity.
Additionally, the diagonal lines formed by the twill weave contribute to the mesh’s flexibility, enabling it to adapt to various shapes and forms.
Reverse Twill Wire Mesh
In contrast to the standard twill mesh, where the wire goes over two and then under two wires consistently, reverse twill mesh inverts this pattern. Each wire alternates by passing under two wires and then over two wires, with the direction of this pattern reversing periodically. This reversal creates a criss-cross effect, contributing to the mesh’s enhanced stability and robustness.
Reverse twill wire mesh is particularly useful in applications where higher loads and finer filtration are required. Its enhanced stability and robustness make it ideal for situations demanding superior strength and durability. Common applications include:
- Filtration Systems: The fine mesh and stable structure are perfect for high-precision filtration, capable of trapping smaller particles while maintaining flow efficiency.
- Industrial Processing: In industrial environments, reverse twill mesh can withstand higher loads, making it suitable for sieving, screening, and sorting materials.
Comparing Strength and Flexibility
The choice between twill and reverse twill often boils down to the specific requirements of strength and flexibility in a project.
Strength
In terms of strength, reverse twill wire mesh typically offers superior durability and load-bearing capability. Due to the reversed pattern, stress is distributed more evenly across the mesh, which makes it less likely to tear and break. As a result, reverse twill is ideal for heavy-duty applications, such as aerospace, mining, and automotive.
Flexibility
The flexibility of twill wire mesh, on the other hand, is greater. In applications such as pharmaceutical and food filters and sieves, its weaving style allows for more movement within the wires, which is beneficial for bending and shaping the mesh.
Applications of Twill vs Reverse Twill Wire Mesh
Each type of wire mesh excels in different applications based on their structural properties:
- Filtration: Both twill and reverse twill are excellent for filtration; however, the choice depends on the size of the particles and the type of load they will bear. Reverse twill is preferable for finer, more abrasive materials due to its enhanced strength.
- Vibration/Shock Absorption: The robust nature of reverse twill makes it suitable for machinery guards and applications requiring high shock absorption.
- Architectural Use: Twill wire mesh is often used in architectural designs due to its aesthetic appeal and flexibility. It can be easily molded into shapes, making it ideal for facades, partitions, and ceiling panels.
- Industrial Sifting: The tight weave of twill mesh makes it suitable for sifting applications in the food, chemical, and mineral industries.
Selecting the Right Mesh for Your Project
Choosing between twill and reverse twill wire mesh involves considering several factors:
- Load Requirements: Evaluate the weight and type of load the mesh needs to support. Heavy or abrasive materials may require the strength of reverse twill.
- Flexibility Needs: If the project demands bending and shaping of the mesh, twill may be the more appropriate choice.
- Environmental Conditions: Consider the environmental conditions the mesh will be exposed to, such as temperatures and corrosive materials, which might affect the longevity and performance of the mesh.
- Budget Constraints: While not significantly different in cost, the choice between twill and reverse twill could be influenced by budget constraints, as the materials and manufacturing processes might vary slightly in price.
Pros and Cons: Twill vs Reverse Twill
Here’s a table outlining the pros and cons of Twill vs Reverse Twill Wire Mesh:
Feature | Twill Wire Mesh | Reverse Twill Wire Mesh |
---|---|---|
Pros | – Increased flexibility | – Enhanced strength and durability |
– Easier to shape and mold | – Better load distribution | |
– Suitable for aesthetic applications | – Superior for fine filtration | |
– Effective for moderate stress conditions | – Ideal for heavy-duty and abrasive materials | |
Cons | – Less durable under high stress | – Less flexible, harder to shape |
– Not ideal for very fine or abrasive materials | – Can be more expensive due to manufacturing | |
– May wear quicker in harsh conditions | – Limited use in aesthetic applications |
Understanding the key differences between twill and reverse twill is crucial when choosing the right wire mesh for your project. Each offers unique strengths and flexibility, making it suitable for specific applications. This guide will help you make an informed decision that ensures the success of your project, maximising both performance and cost-efficiency.
The right type of wire mesh can make a big difference in your final product’s functionality and durability, whether you choose reverse twill or twill.
As always, thank you for checking out our blog. We hope that this helps you with your project. We try to launch a couple of new guides every week. Eventually we will have covered everything there is to cover about mesh.
You may be interested in our blog that explores metal mesh vs plastic mesh.
Our goal for our blogs and help guides is to answer as many questions as possible to help to explain the possibilities of mesh to our customers.
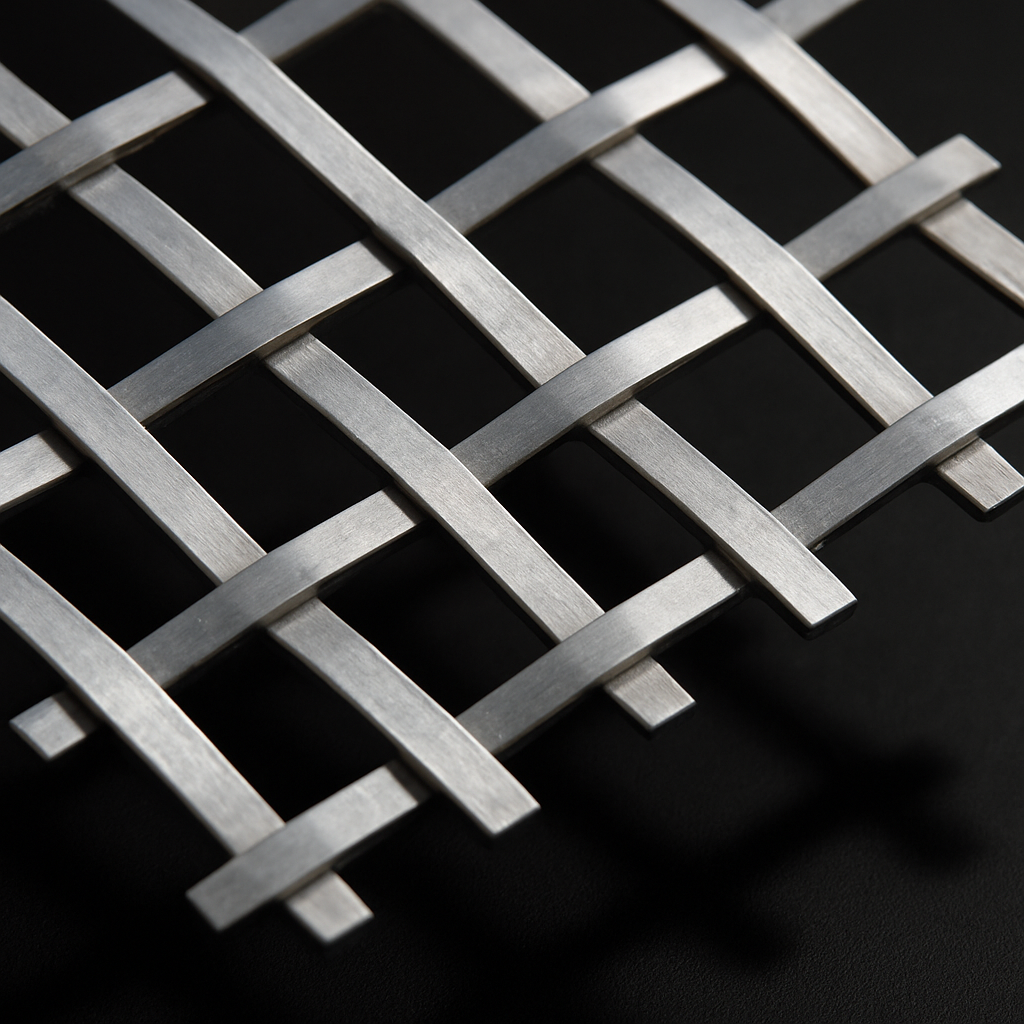
What Is Lattice Mesh and Why Choose Stainless Steel 304?

Introducing Our Brass-Coloured Aluminium Lattice Weave Mesh: Style Meets Practicality
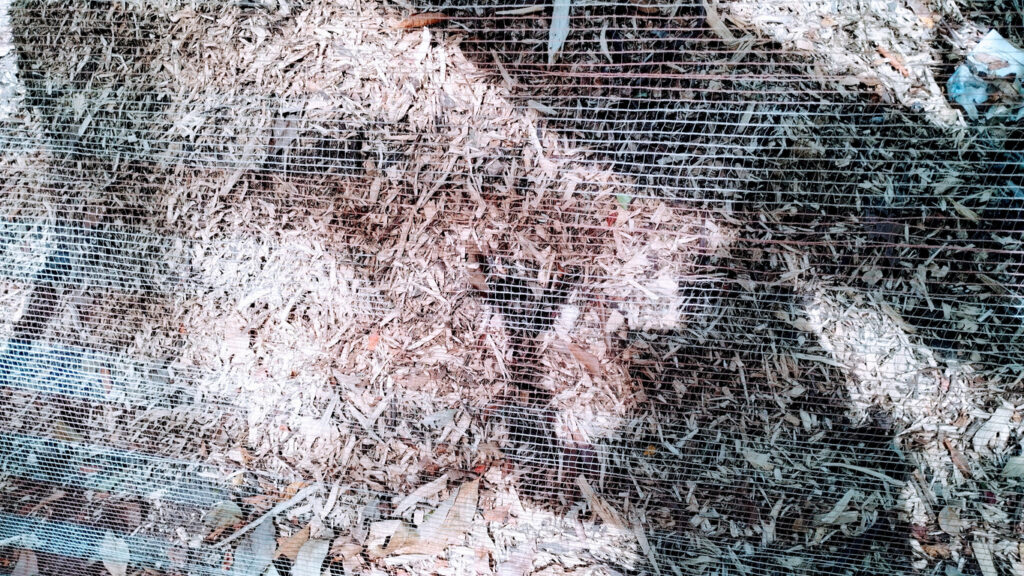
How Vent Mesh Protects Against Rodents and Debris
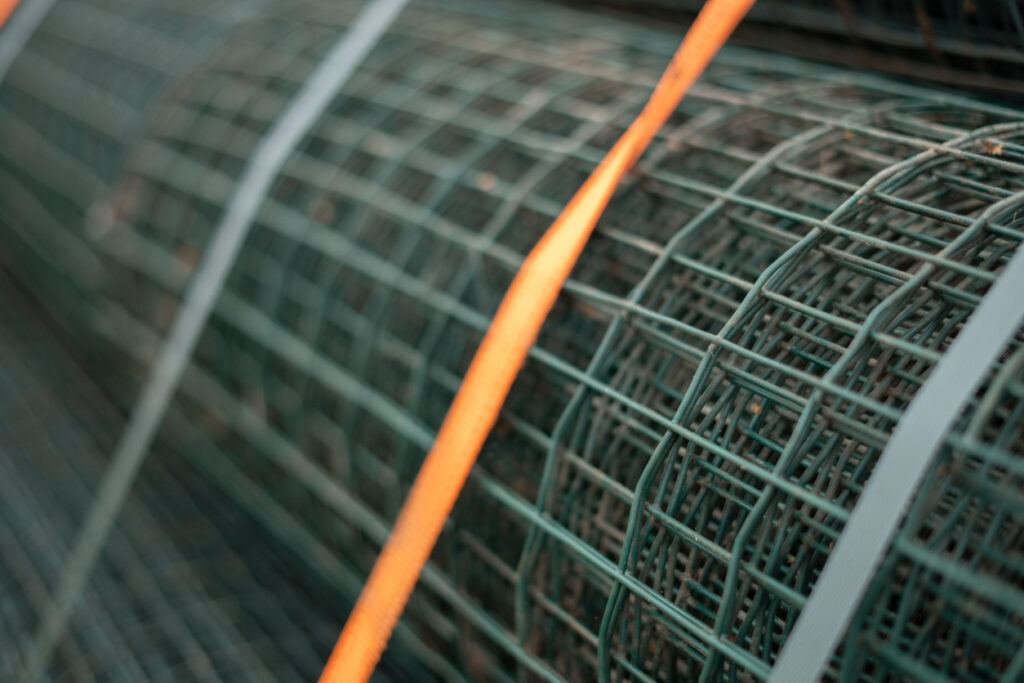
Benefits of PVC-Coated Galvanised Steel Fencing: Strong, Stylish, Long-Lasting
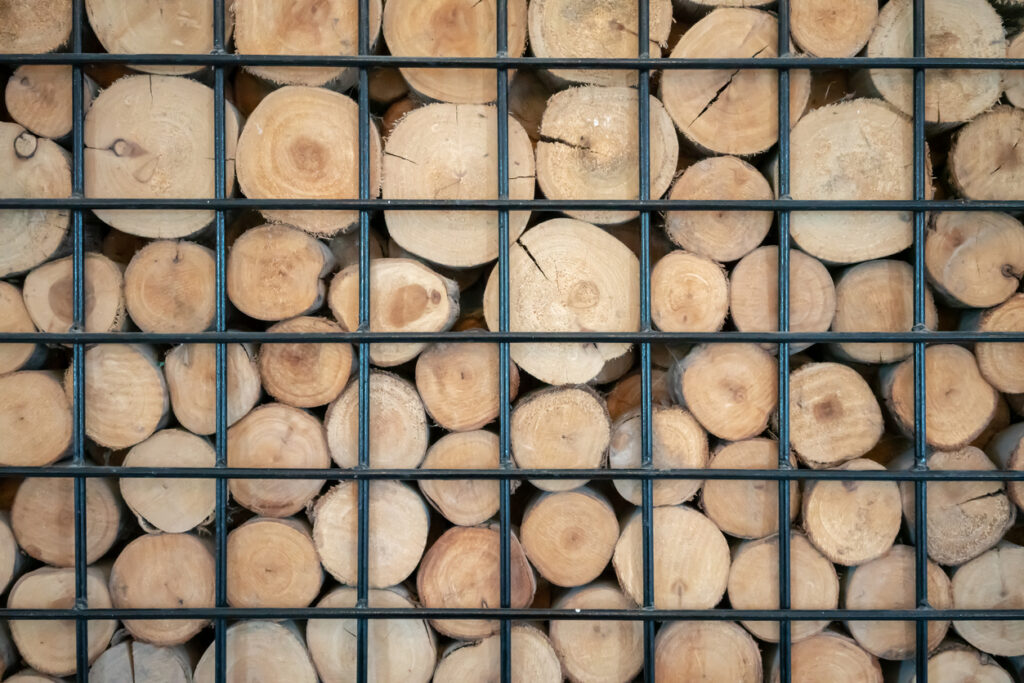
Firewood Mesh: Keeping Your Logs Dry and Secure
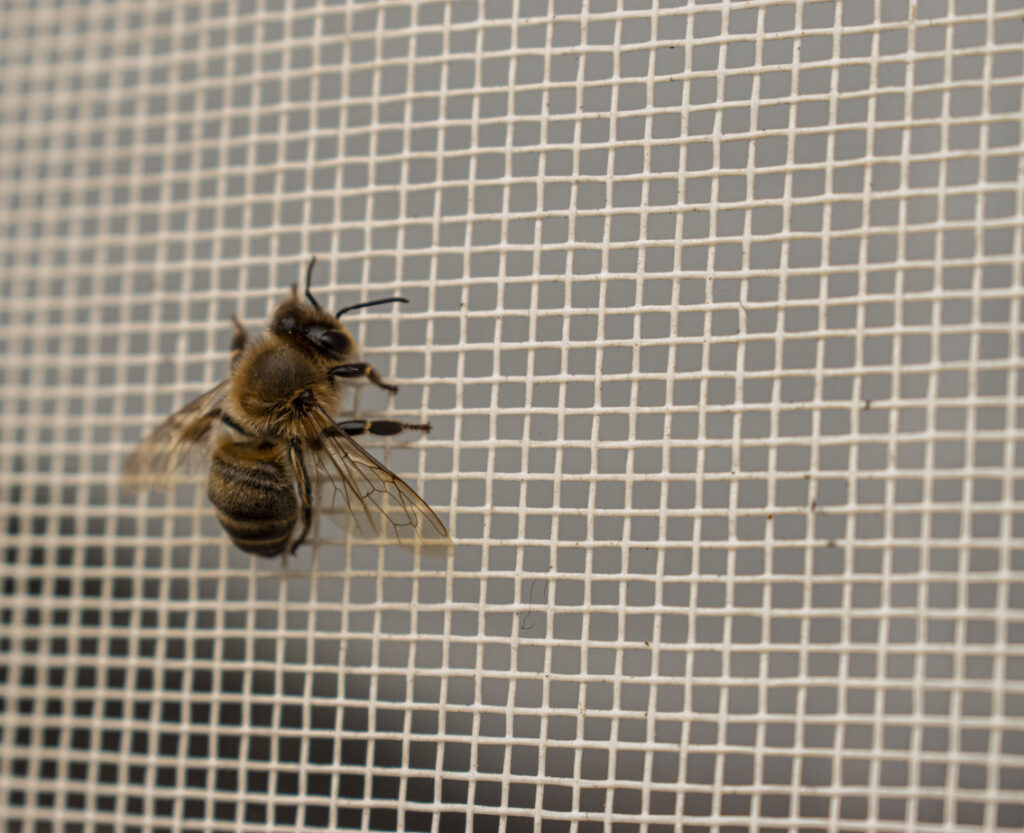
Hive Mesh for Beekeeping: Safer Hives with Stainless Steel Mesh
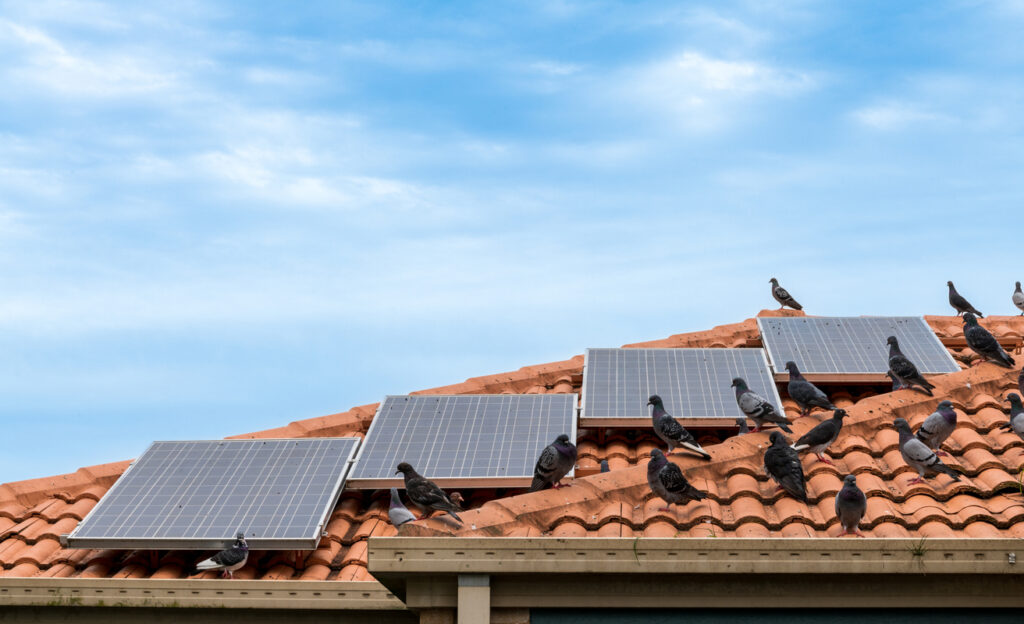
How To Use Solar Panel Mesh to Stop Birds Nesting Underneath
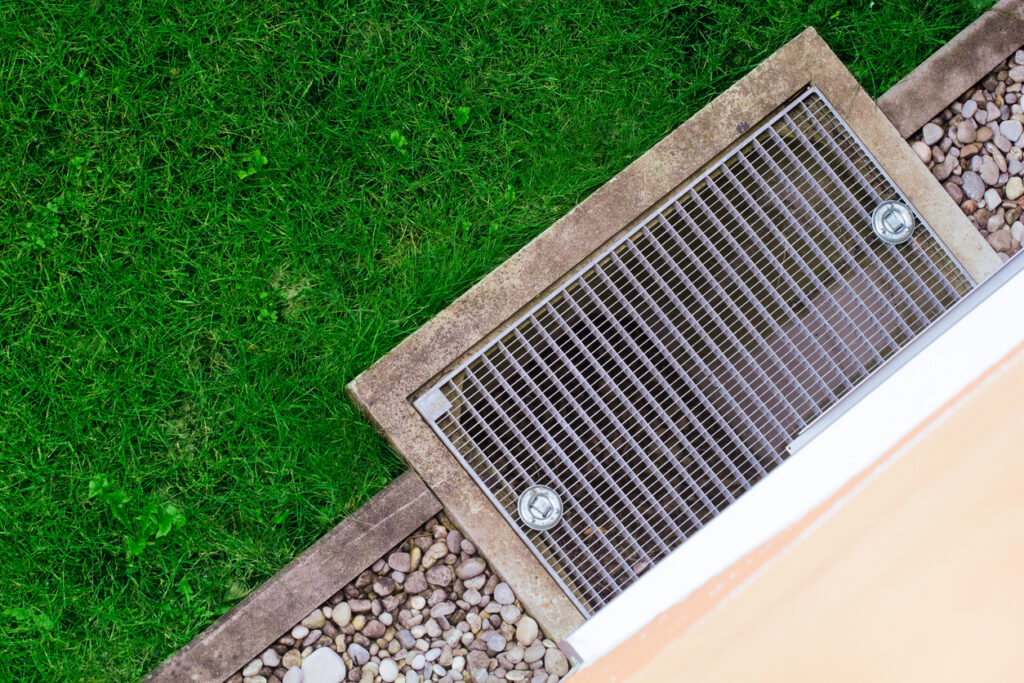
Choose the right stainless steel mesh for outdoor drainage.
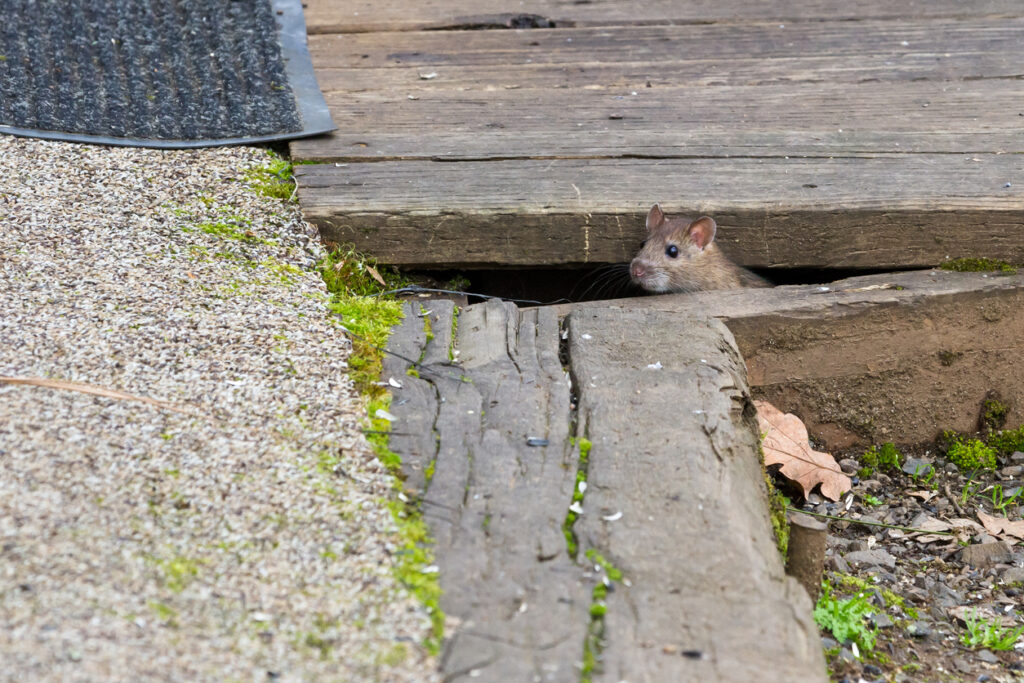