Expanded metal lath has become an indispensable material in various construction and architectural projects, thanks to its strength, versatility, and aesthetic appeal.
At the core of the successful utilisation of this material is the skillful art of cutting and shaping, particularly when working with specific types such as 10 x 8mm mild steel expanded metal.
In this super comprehensive guide, we will delve into expert techniques and tips to ensure you achieve precision and efficiency in your projects.
Let’s get into it…
Understanding 10 x 8mm Mild Steel Expanded Metal
Before diving into the techniques, it’s crucial to understand the properties and applications of 10mm mild steel expanded metal.
Mild steel, known for its ductility and malleability, is an ideal material for creating expanded metal.
The 10 x 8mm size refers to the size of the openings in the mesh, offering a balance between strength and open area, making it perfect for a range of applications including cladding, security panels, and filtration systems.
Advantages of Using Mild Steel Expanded Metal:
- Durability: Resistant to impact and wear.
- Flexibility: Can be easily shaped and formed.
- Aesthetic Appeal: Offers a unique industrial look.
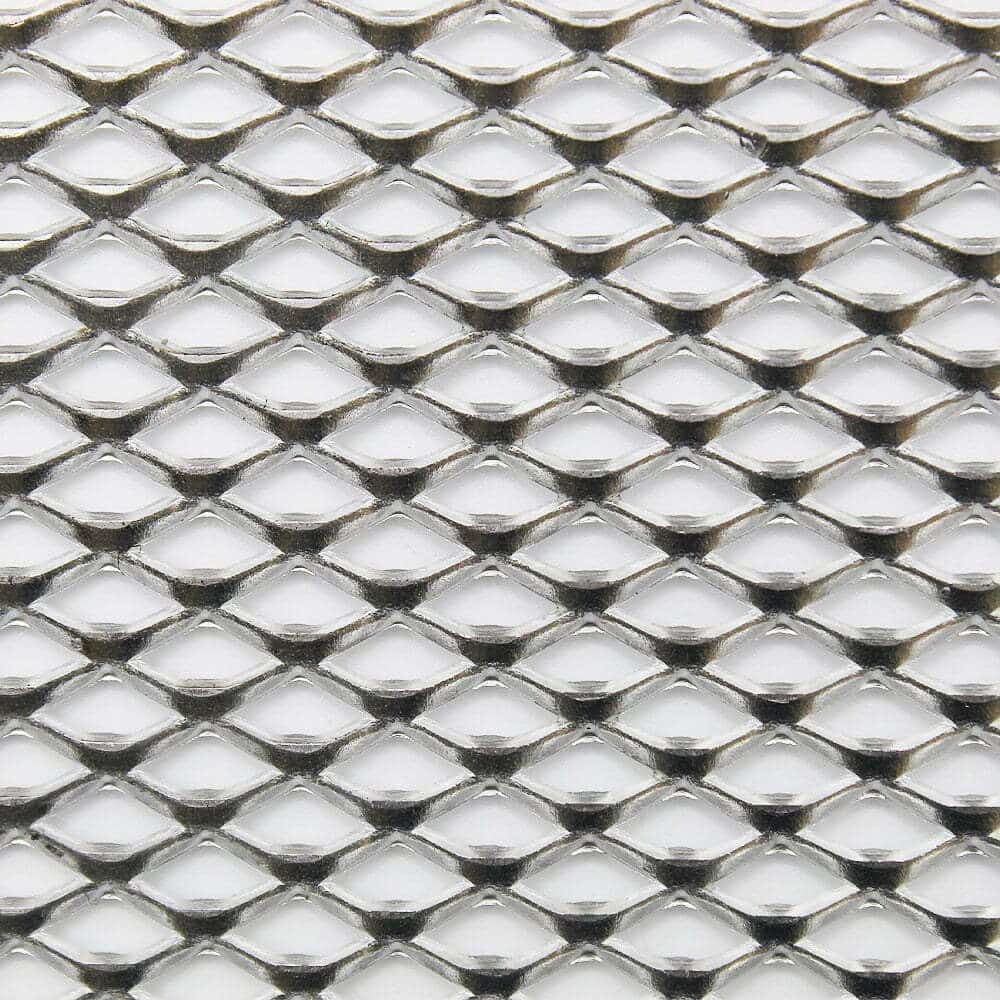
Tools and Safety Gear
Before starting your project, ensure you have the right tools and safety gear.
For cutting and shaping expanded metal lath, you will need:
- Metal shears or a nibbler
- Angle grinder with a metal cut-off wheel
- Bench shears for straight cuts
- Protective gloves, goggles, and hearing protection
Cutting Techniques for Precision and Clean Edges
For both functionality and aesthetics, it is crucial to achieve precision and clean edges when working with 10 x 8mm mild steel expanded metal.
Here are detailed techniques to help you accomplish this:
1. Marking Your Cut:
- Preparation: Begin by thoroughly cleaning the surface of the metal to ensure clear visibility of markings.
- Using Chalk Line or Marker: A chalk line can provide an accurate guide for long, straight cuts. Use a fine-tipped marker for intricate designs or curves. To ensure accuracy in your final cut, be precise with your markings.
- Double-Checking Measurements: Don’t forget that measuring twice and cutting once is always a better idea. As a result, you will waste less material and your cuts will be in accordance with the project requirements.
2. Using Metal Shears or Nibbler:
- Manual Metal Shears: When it comes to cutting thinner sheets of expanded metal, manual shears provide the best control and ease of use, making them ideal for smaller or more demanding jobs. This kind of tool is especially useful when you need to cut shapes or if you want to do projects that require a more hand-on approach.
- Electric Nibbler: An electric nibbler can be more suitable when dealing with denser parts of the mesh or for prolonged use. With it, precise cuts can be made without distorting the material and complex shapes can be cut out easily.
- Technique: Use either tool slowly and steadily, following the marked line closely. To prevent jagged edges, keep the cutting blades sharp and well-maintained.
3. Employing an Angle Grinder:
- Tool Selection: Choose an angle grinder with an appropriate metal cut-off wheel. Ensure the wheel is suited for the thickness and material type of your expanded metal.
- Safety Precautions: When using an angle grinder, always wear protective gear, including gloves and eye protection. Be aware of the sparks and debris that will be produced and keep a steady hand.
- Cutting Process: Start the cut by aligning the grinder with the marked line. Keep a steady pace and apply consistent pressure to ensure a straight and clean cut. Don’t force the grinder through the metal; let it do its job.
4. Bench Shears for Straight Cuts:
- Ideal for Long, Straight Cuts: Long, straight, and precise cuts can be made with bench shears. Particularly useful in projects requiring uniformity and straight edges.
- Operation: Secure the metal lath firmly against the edge guide of the bench shear. Apply steady pressure on the handle to create a clean cut. For longer sheets, it may be necessary to make multiple cuts.
- Advantages: During cutting, bench shears provide a stable platform, reducing the risk of metal buckling or bending. For professional-grade straight edges, this stability is essential.
Shaping Techniques for Expanded Metal
The process of shaping expanded metal, especially mild steel 10 x 8mm, involves both art and science. To mold a material into a desired shape, it is necessary to understand its properties and employ the right techniques.
Here’s a detailed look at some shaping methods:
1. Bending and Forming:
- Using a Vise and Hammer: Clamping the metal in a vise and gently shaping it with a hammer works well for smaller or more intricate bends. Custom or unique bends can be created using this method because it allows for a high degree of control.
- Metal Brake for Consistent Bends: Metal brakes are invaluable when you need consistent, straight, or long bends. In projects requiring consistency, it ensures uniformity and precision.
- Technique Tips: To avoid overstressing the metal, bend gradually. Using heat to assist in bending thicker sections is possible, but should be done cautiously to maintain the integrity of the metal.
2. Rolling for Curves:
- Using a Sheet Metal Roller: Smooth, consistent curves can be created with a sheet metal roller. Particularly useful in architectural applications requiring aesthetic uniformity.
- Process: With each pass, adjust the rollers to increase the bend of the expanded metal. Templates can be used as guides for complex curves.
- Considerations: Be aware of the metal’s natural tendency to spring back slightly after bending when rolling. To achieve the desired final shape, the metal must be overbent slightly due to its ‘elastic recovery’.
3. Joining and Welding:
- Spot Welding for Joining: Spot welding is often used to join expanded metal pieces. A strong bond is achieved without overheating the entire piece.
- Alignment and Clamping: Align the pieces properly before welding. During welding, clamps should be used to hold the pieces in place.
- Welding Technique: To prevent warping or damage to the metal, keep the welding time short. Before you work on your final piece, practice on scrap pieces to get the settings and timing right.
Tips for Working with Expanded Metal Lath
- Measure Twice, Cut Once: Accurate measurements are vital. This not only reduces waste but also ensures that the pieces fit perfectly in your final assembly.
- Maintain Tools: Regularly check and maintain your tools. Dull tools can cause poor cuts or require more effort to use, leading to potential inaccuracies.
- Safety First: Always prioritize safety by wearing protective gear and working in a well-ventilated area, particularly when welding or cutting.
- Understand Material Properties: Knowledge of how mild steel reacts to different processes will help you anticipate challenges and adjust your techniques accordingly.
Finishing and Protective Measures
After the cutting and shaping phase, finishing and protection are crucial to ensure both aesthetic appeal and longevity of the metal:
1. Deburring Edges:
- Using the Right Tool: Smooth any sharp or rough edges with a file or a specialized deburring tool. For safety reasons and to finish your project professionally, this step is crucial.
- Attention to Detail: To ensure a thorough finish, pay attention to all edges, even those that aren’t immediately visible.
2. Coating and Painting:
- Primer and Paint: The metal should be primed and painted to prevent corrosion, especially if it will be exposed to the elements. Paint should be chosen according to the metal and the conditions it will be exposed to.
- Weather-Resistant Coatings: You can extend the life of metal by using a coating that is resistant to weather, UV rays, and temperature changes.
3. Regular Maintenance:
- Inspections: Regularly inspect your expanded metal installations for signs of wear, corrosion, or damage.
- Prompt Repairs: Address any issues immediately to prevent further deterioration. This includes touching up paint or coatings as necessary.
Using these shaping techniques and following these tips, you can create high-quality, durable, and aesthetically pleasing designs and structures out of mild steel expanded metal 10 x 8mm.
Your final product’s quality is greatly influenced by how well you shape and finish it.
As always, thank you for checking out our blog. We hope that this helps you with your project. We try to launch a couple of new guides every week. Eventually we will have covered everything there is to cover about mesh.
You may be interested in our blog that explores mild steel perforated sheet metal.
Our goal for our blogs and help guides is to answer as many questions as possible to help to explain the possibilities of mesh to our customers.
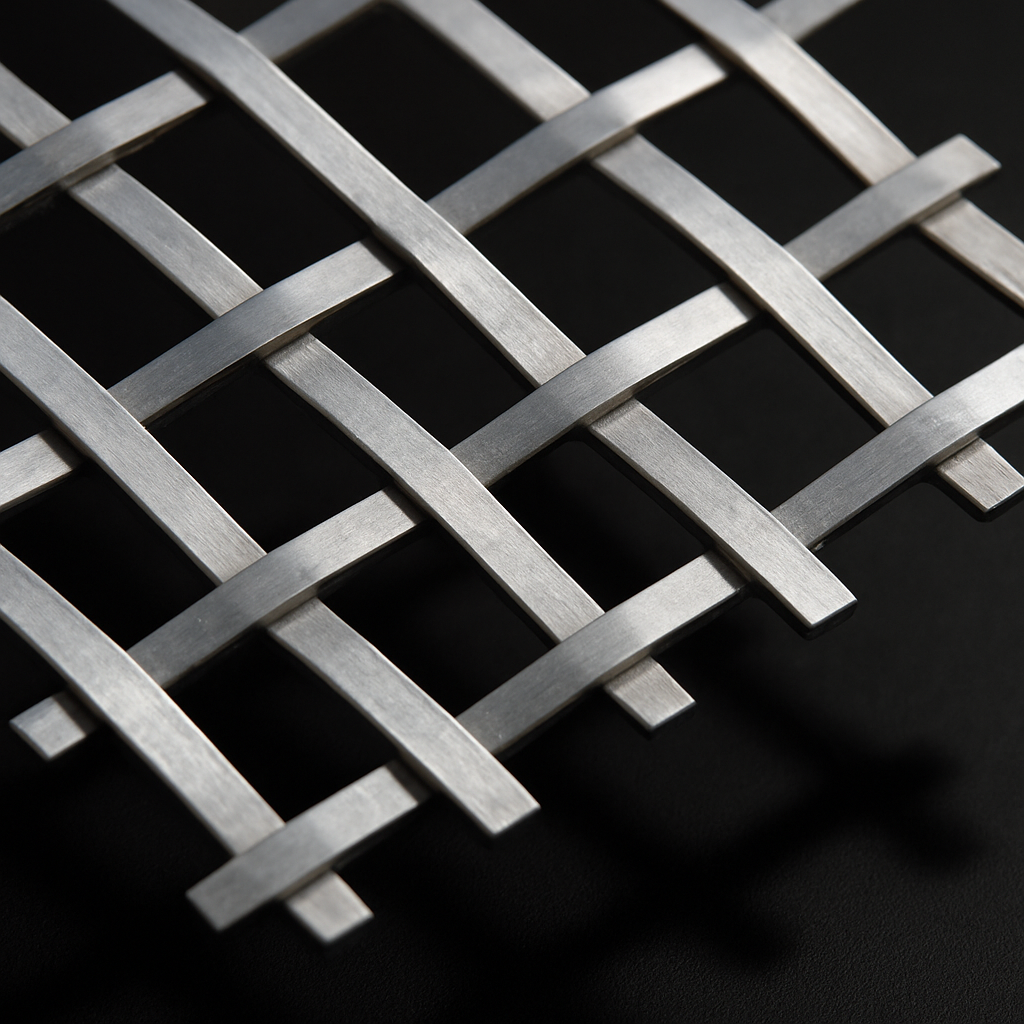
What Is Lattice Mesh and Why Choose Stainless Steel 304?

Introducing Our Brass-Coloured Aluminium Lattice Weave Mesh: Style Meets Practicality
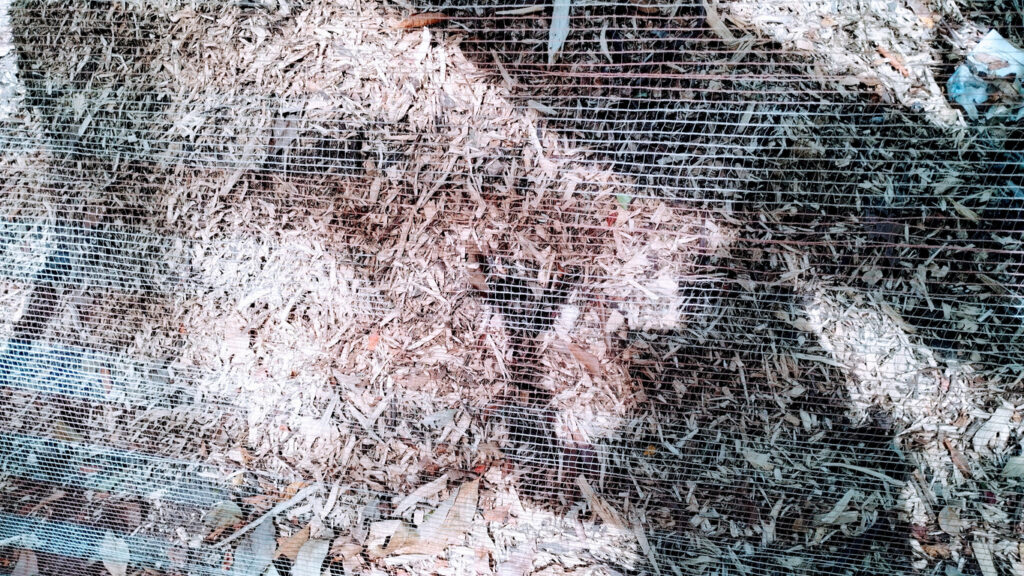
How Vent Mesh Protects Against Rodents and Debris
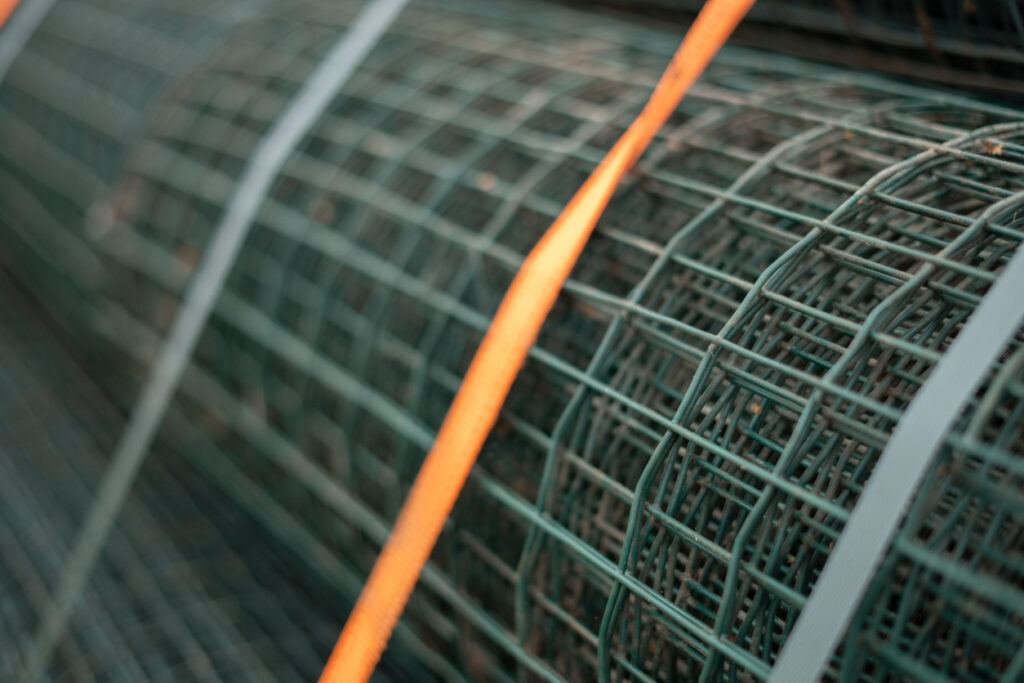
Benefits of PVC-Coated Galvanised Steel Fencing: Strong, Stylish, Long-Lasting
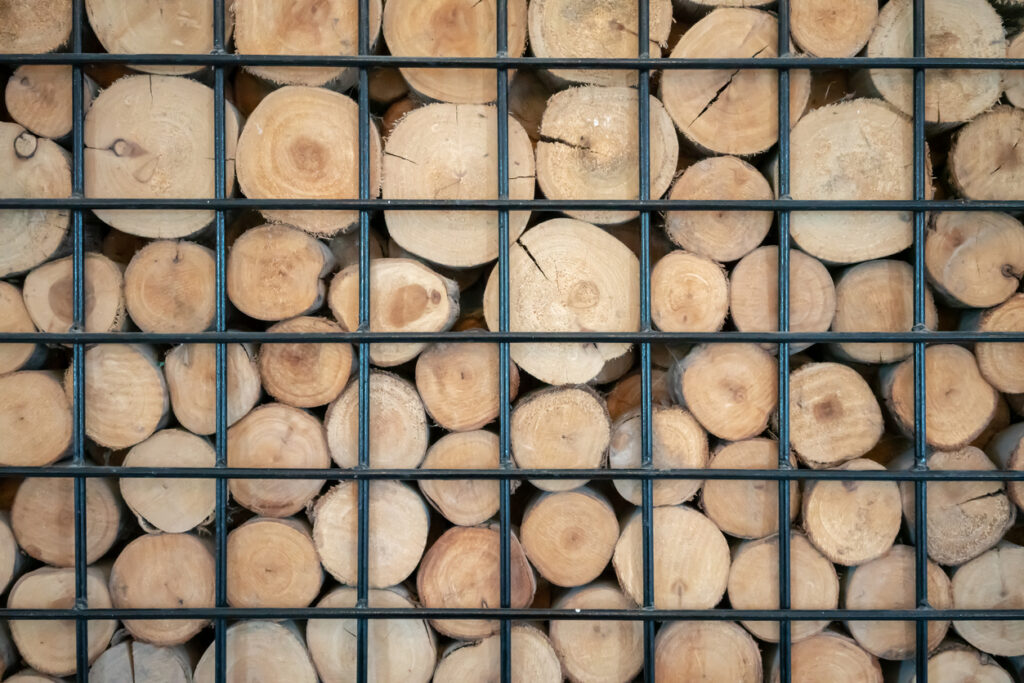
Firewood Mesh: Keeping Your Logs Dry and Secure
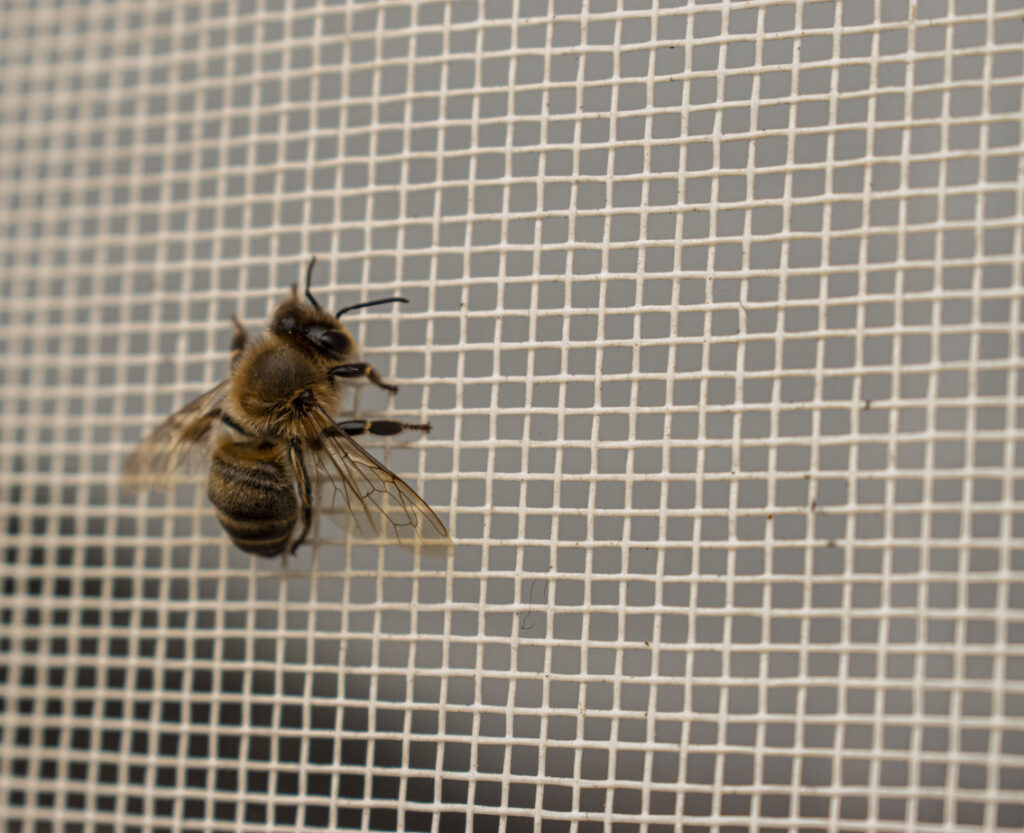
Hive Mesh for Beekeeping: Safer Hives with Stainless Steel Mesh
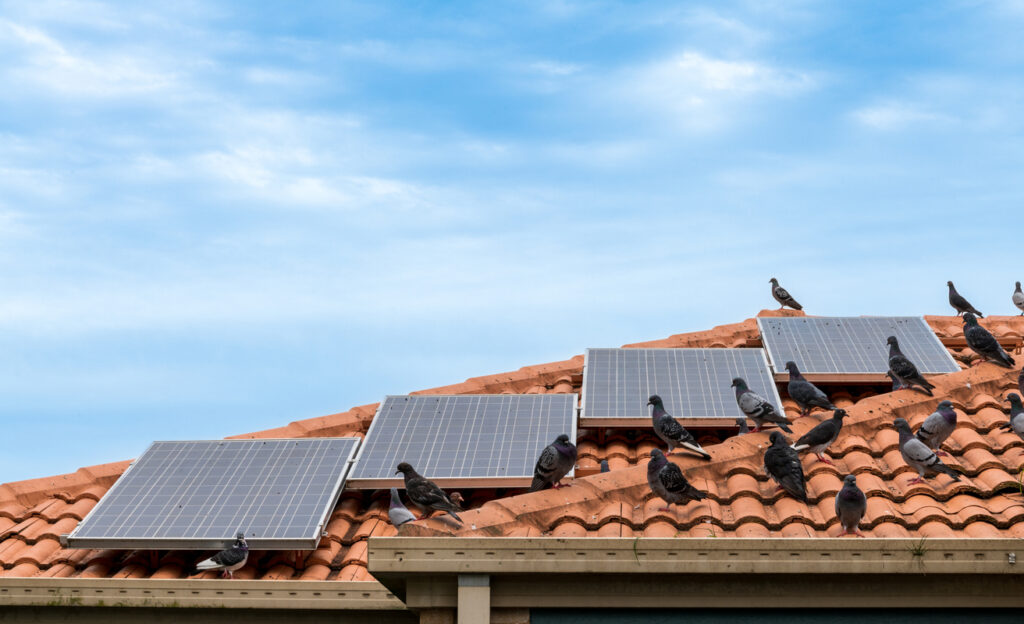
How To Use Solar Panel Mesh to Stop Birds Nesting Underneath
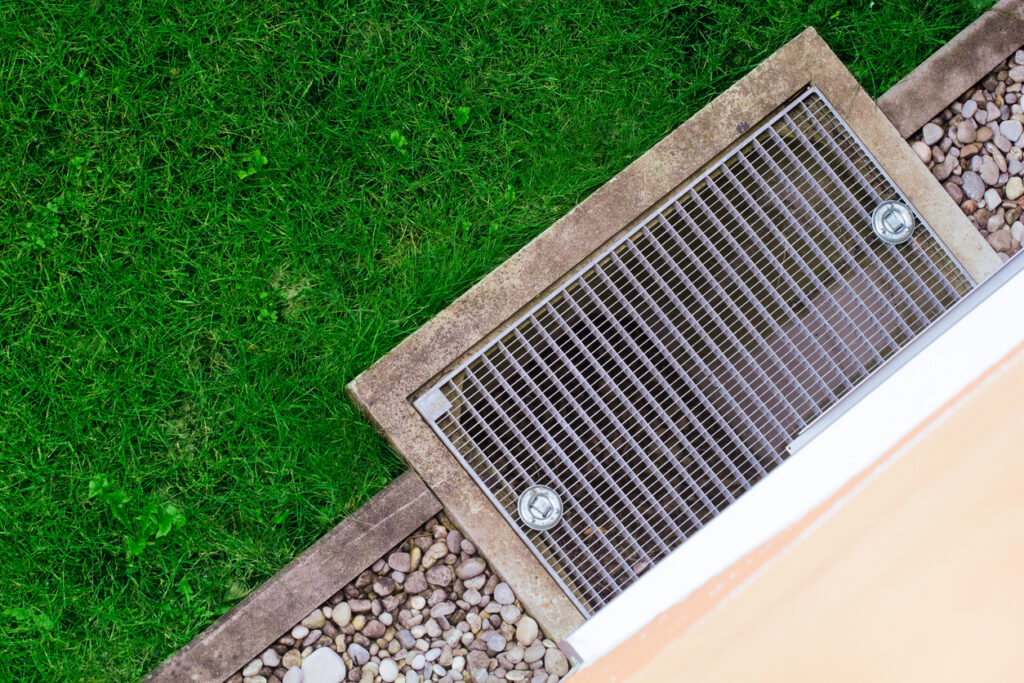
Choose the right stainless steel mesh for outdoor drainage.
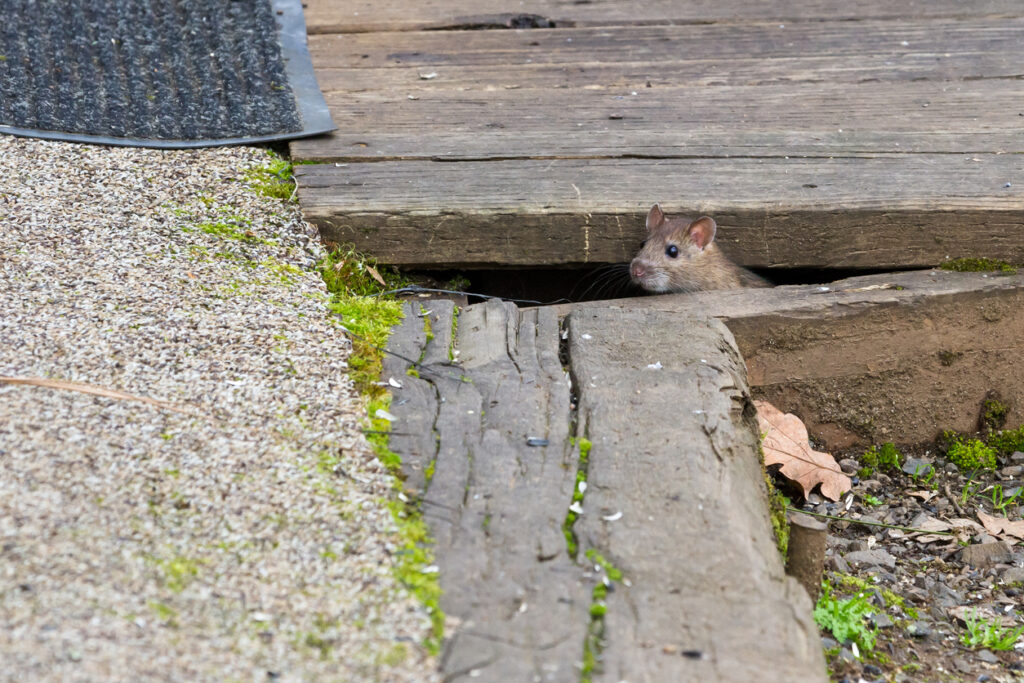