Perforated metal sheet is an increasingly popular material for acoustic applications.
It is a versatile and cost-effective solution that can be used to improve sound clarity and dampen noise levels.
Let’s take a quick look at why perforated metal sheet is so beneficial for acoustic applications.
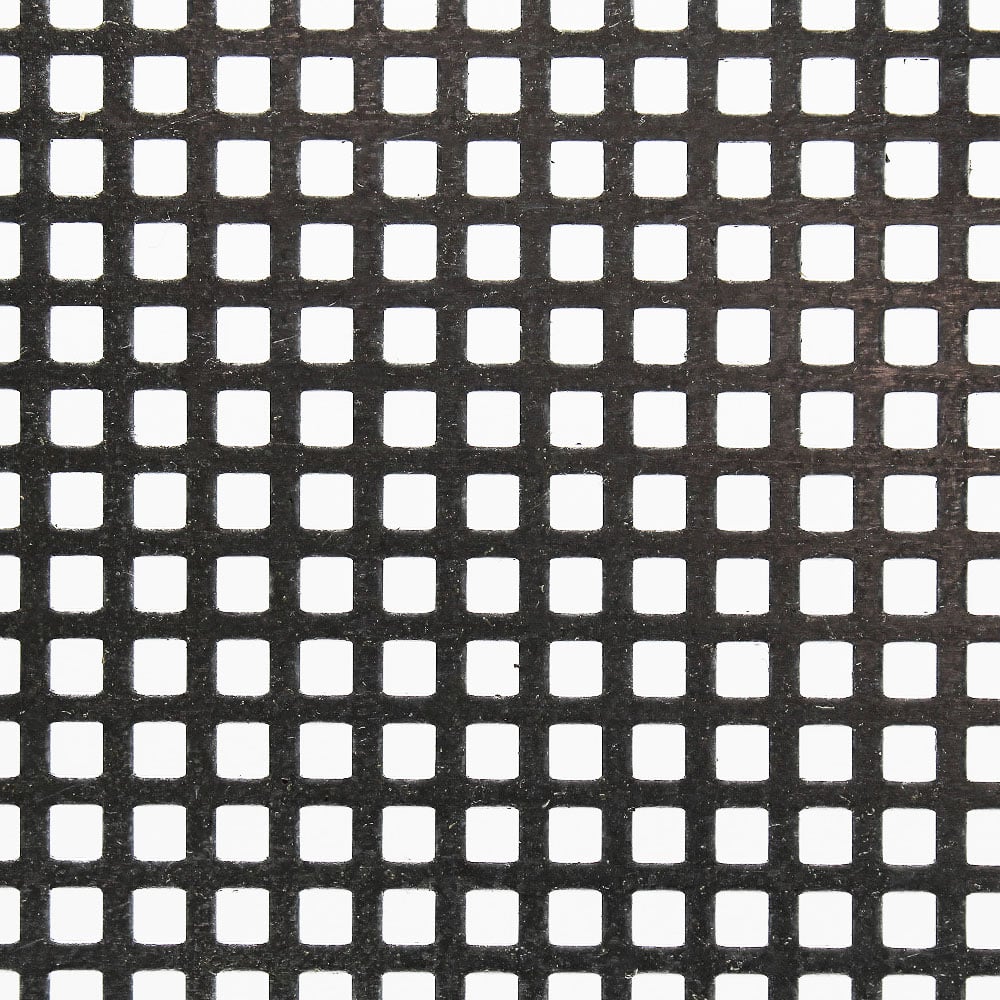
What's The Science?
When sound waves pass through perforated metal panels, some of the energy is absorbed by the material and the air within the holes. This reduces the amount of sound that is reflected back into the space, thereby decreasing overall noise levels. The effectiveness of sound absorption depends on factors like hole size, open area, and panel thickness. Additionally, adding an acoustic backing material (e.g., mineral wool, foam, or fibreglass) behind the perforated metal panels can further enhance sound absorption by trapping and dissipating sound waves.
Perforated metal panels can scatter sound waves in various directions, creating a more even distribution of sound energy throughout the space. This is particularly beneficial in applications like concert halls or theatres, where it’s essential to achieve a balanced sound experience. The diffusion of sound waves depends on the perforation pattern, hole size, and panel arrangement. Irregular patterns or varying hole sizes can help disperse sound waves more effectively, preventing the formation of focused sound reflections or echoes.
While perforated metal panels primarily absorb and diffuse sound, they can also reflect sound waves depending on their configuration. This can be useful in applications where it’s necessary to direct sound towards specific areas or create an acoustic barrier. Factors that influence sound reflection include material type, panel thickness, and hole size. Smaller holes and a lower open area percentage generally result in a higher degree of sound reflection.
Determine The Purpose
Before you begin, you must identify the specific acoustic requirements for your project, such as sound absorption, diffusion, or reflection. This will guide your choice of perforated metal pattern, hole size, and material thickness.
Choose The Right Material
Select a suitable material for your perforated metal, such as aluminium, steel, or stainless steel. Consider factors like corrosion resistance, weight, and aesthetics.
Consider factors like corrosion resistance, weight, and aesthetics. The choice of material can affect the overall acoustic performance and durability of the installation.
The open area is the percentage of the metal sheet with holes relative to the total surface area. A higher open area usually results in better sound absorption. Consider the balance between open area and structural integrity when selecting a perforated metal sheet.
The thickness of the perforated metal sheet can impact its sound absorption capabilities and structural strength. Thicker materials are more rigid and can support larger panels, while thinner materials may require additional support or framing.
Select The Perforation Pattern
Choose a perforation pattern that meets your acoustic needs. Patterns with smaller holes and a higher percentage of open area typically provide better sound absorption. For sound diffusion, opt for irregular patterns or varying hole sizes.
We specialise in round, square and hexagonal for this purpose.
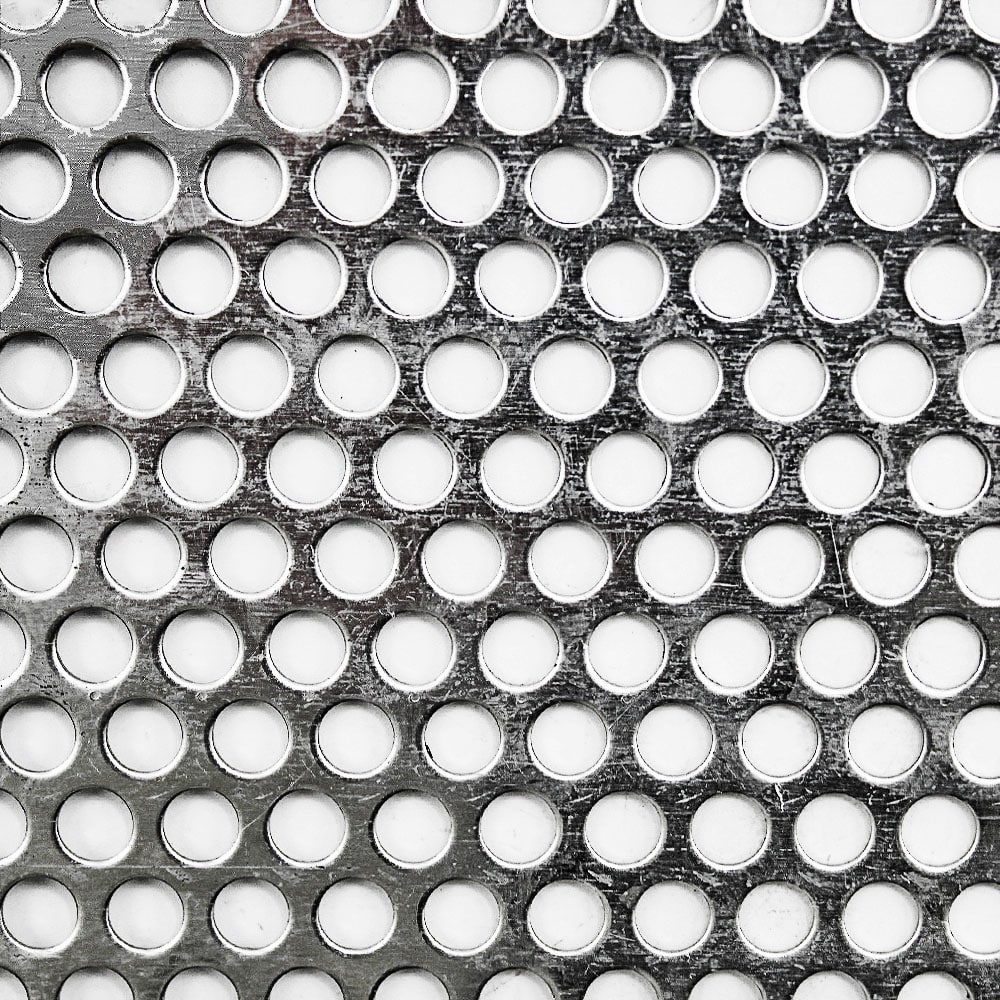
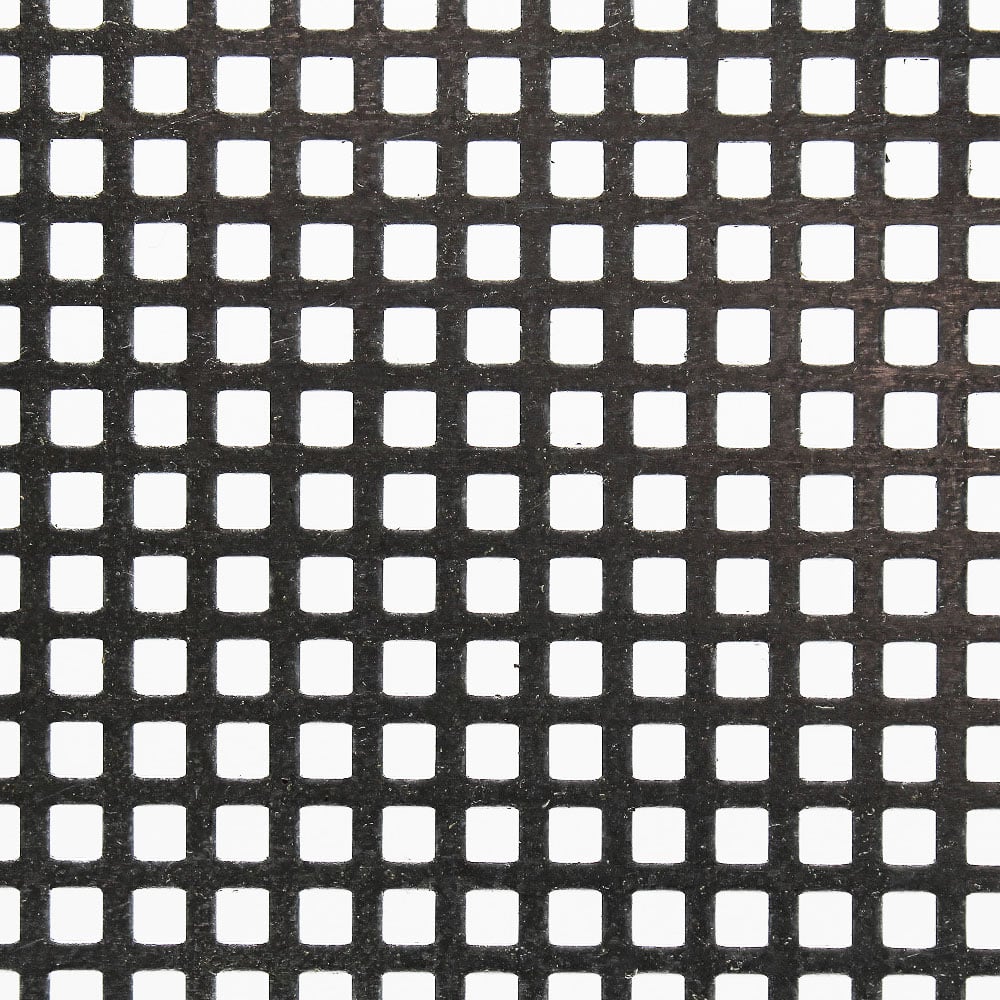
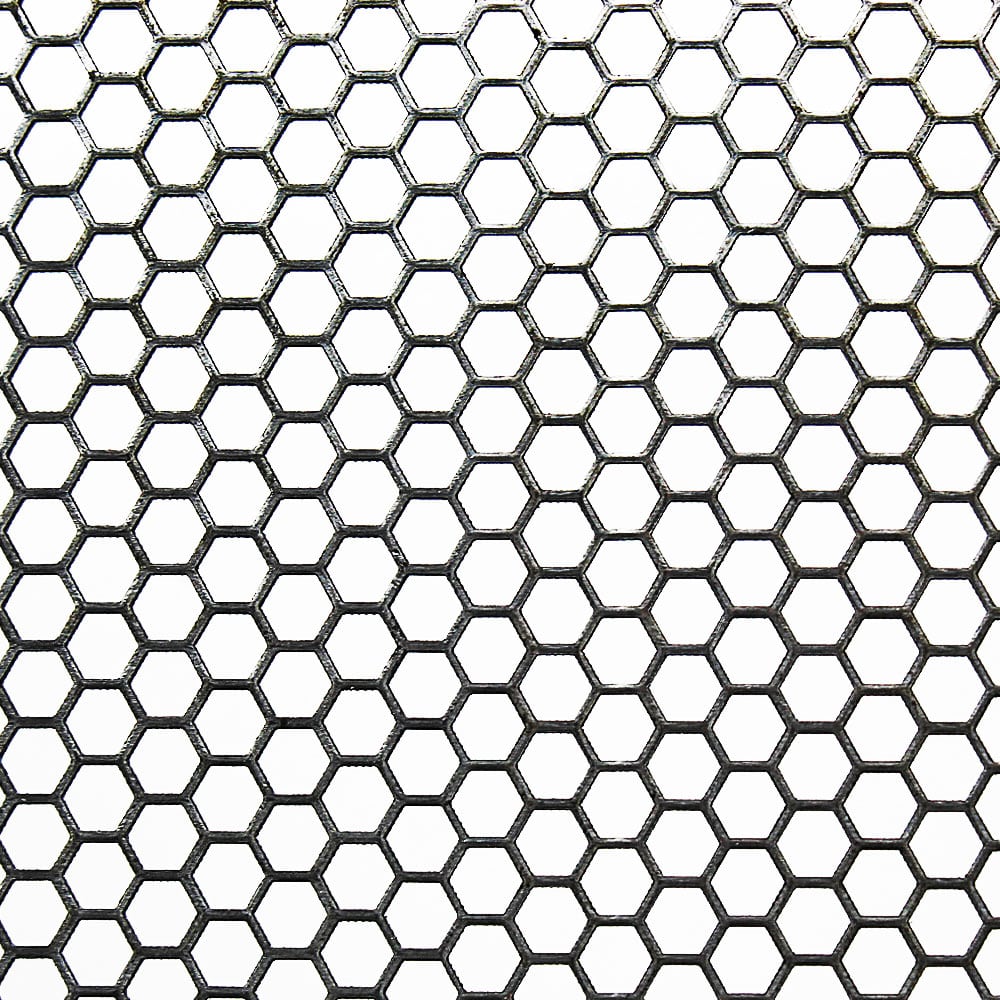
Should I Add Acoustic Backing Material?
To enhance sound absorption, consider adding an acoustic backing material, like mineral wool, foam, or fibreglass, behind the perforated metal panels. This will help trap and dissipate sound waves.
- Adhesive: Apply a suitable adhesive (such as a spray adhesive or construction adhesive) to the back of the perforated metal panel, then press the backing material onto the adhesive, ensuring full contact and a secure bond.
- Mechanical fasteners: Use mechanical fasteners, such as clips or screws with washers, to attach the backing material to the perforated metal panels. Ensure the fasteners are spaced evenly and don’t compress the backing material too much, as this can reduce its acoustic performance.
- Acoustic frame or sandwich panel: You can also create a sandwich panel by placing the backing material between two perforated metal sheets, or use an acoustic frame to hold the backing material in place behind the perforated metal.
Plan The Installation
Plan the layout of your perforated metal panels and determine the necessary mounting system.
As outlined above you must consider factors such as the location, panel size, and weight, as well as any insulation or backing material.
We can help with this if you require any assistance at all with the planning.
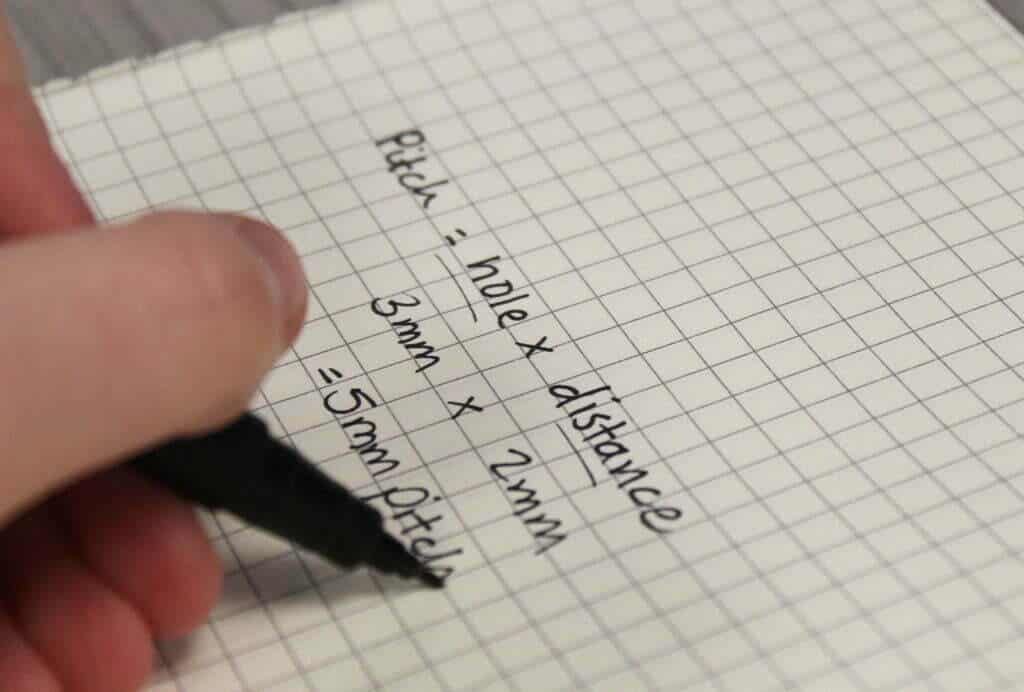
Mount The Panels
Install the perforated metal panels according to your plan, ensuring they are securely fastened to the mounting system. If using an acoustic backing material, make sure it is properly positioned behind the panels.
Choose the mounting system: Select an appropriate mounting system for your perforated metal panels, such as direct screw fastening, Z-clip systems, or suspended mounting with cables or rods. Consider factors like panel size, weight, and desired alignment when choosing your mounting method.
Mark the mounting locations: Based on your layout plan, mark the positions of the mounting points on the walls, ceiling, or support structure where the perforated metal panels will be installed. Ensure that the mounting points are evenly spaced and level to guarantee proper alignment and support.
Install the mounting hardware: Attach the mounting hardware (such as brackets, clips, or rails) to the marked locations, following the manufacturer’s instructions and ensuring they are securely fastened and level.
Seal Gaps & Joints
To maximize the effectiveness of your acoustic application, seal any gaps or joints between panels using appropriate sealants or gaskets.
Test & Adjust
Once the installation is complete, test the acoustic performance of the space. If necessary, make adjustments by adding more perforated metal panels, changing the perforation pattern, or modifying the backing material.
Any you’re done.
By following these steps, you can effectively use perforated metal for a range of acoustic applications, such as soundproofing rooms, reducing noise in industrial environments, or improving the acoustics in theatres and concert halls.
As always, thank you for checking out our blog. We hope that this helps you with your project. We try to launch a couple of new guides every week. Eventually we will have covered everything there is to cover about mesh.
Our goal for our blogs and help guides is to answer as many questions as possible to help to explain the possibilities of mesh to our customers. Contact our team today if you have any questions at all. We are always really keen to help in any way that we can.
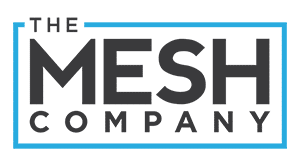