In the world of industry, architecture and design, the choice of materials plays a pivotal role.
When it comes to perforated screens, two heavyweights dominate the scene: aluminium and steel. Both offer a range of benefits, but which one should you choose for your next project?
This article intends to elaborate on which is best in several areas and try to come to an overall winner.
Let’s get into it….
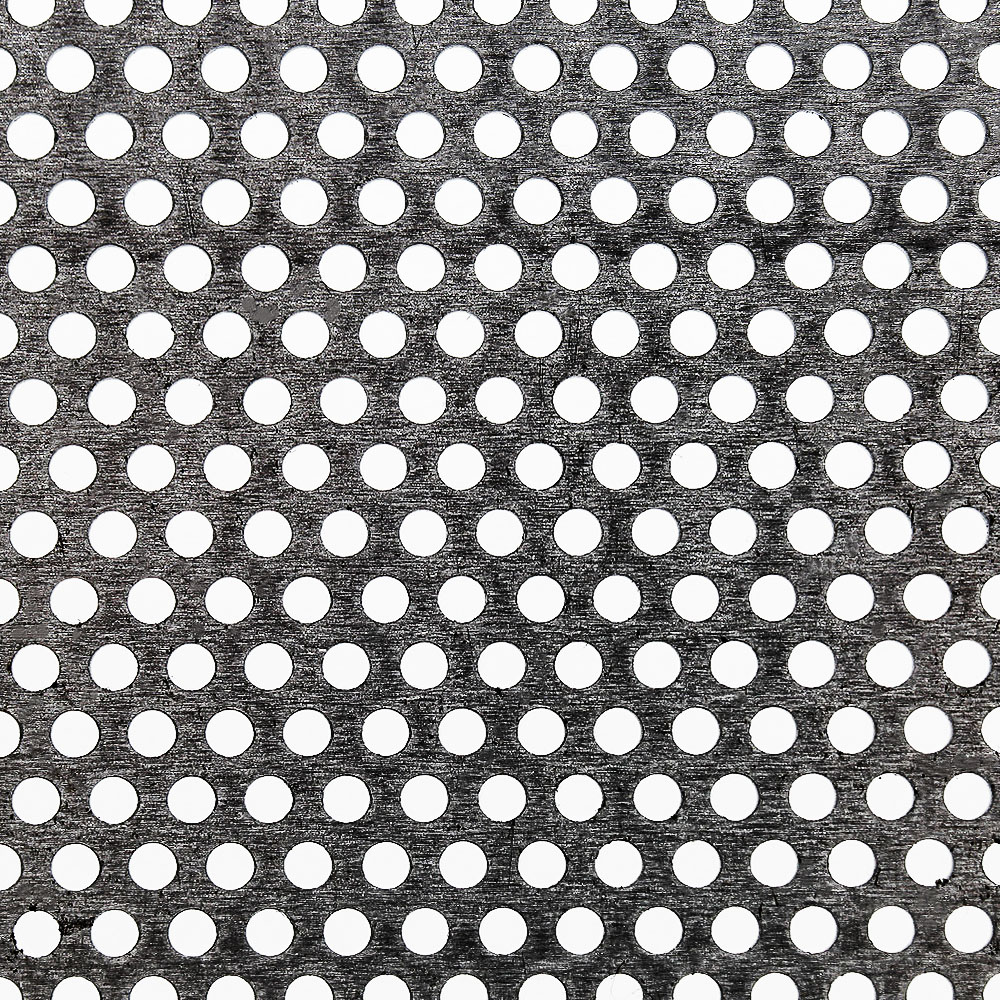
Aluminium: The Modern Marvel
Aluminium, often referred to as the ‘metal of the future’, boasts an array of properties that make it a standout material for various applications.
One of the most significant advantages of aluminium is its weight – or rather, the lack thereof. Aluminium is approximately one-third the weight of steel, making it an excellent choice for applications where reduced weight is crucial, like in transportation or aerospace sectors. This lightweight nature doesn’t compromise its strength, and aluminium can be reinforced with various alloys to suit specific requirements.
Corrosion resistance is another hallmark of aluminium. Its ability to naturally form a protective oxide layer when exposed to air ensures it stands up well against the elements. This is especially beneficial for outdoor applications, where materials are subjected to varied environmental conditions. Plus, when anodized, aluminium not only gains additional corrosion resistance but also offers a range of attractive finishes, enabling designers to achieve both functional and aesthetic goals.
Beyond its physical properties, aluminium resonates with modern industries because of its environmental credentials. Being highly recyclable, it’s a material of choice in the green building and sustainable design sectors. Its production, while energy-intensive, is offset by the metal’s longevity and the fact that recycling aluminium requires only 5% of the initial energy consumed to produce it.
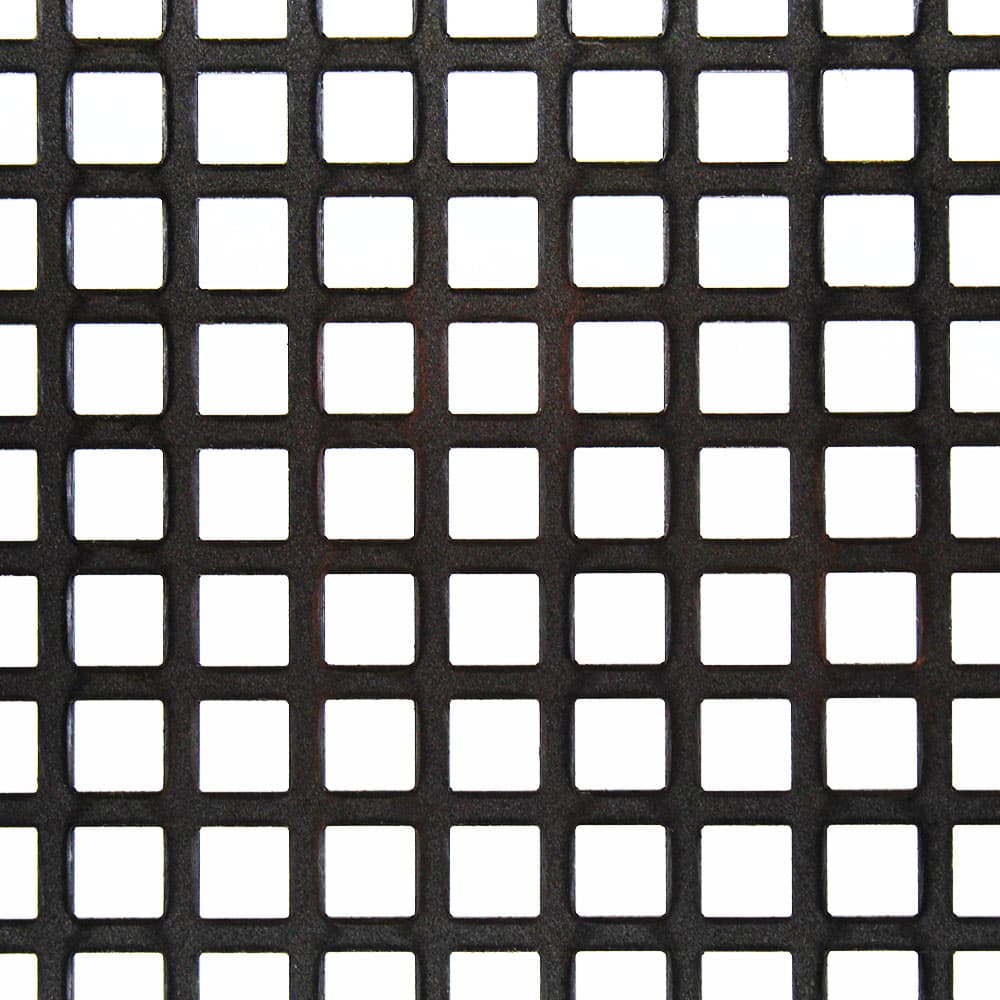
Steel: The Time-Tested Titan
Steel, an alloy primarily made of iron and carbon, has a storied history as one of the pillars of modern civilization.
Its impressive tensile strength and durability have made it the backbone of infrastructures, from towering skyscrapers to sprawling bridges. Steel’s robustness is particularly useful in environments that demand resilience, making it a preferred choice for heavy-duty applications, security barriers, and protective screens.
Steel has the advantage of being versatile. There are a variety of steel grades available, ranging from carbon steel to alloy and stainless steel. The corrosion resistance of stainless steel, in particular, rivals that of aluminium in certain conditions. In applications such as kitchen appliances, medical equipment, and architecture, it is invaluable.
Raw steel can evoke a sense of industrial ruggedness, but it is not limited to that. Designers can leverage steel’s strength without compromising its visual appeal by coating, painting, or treating it.
Steel has merits when it comes to sustainability. A significant percentage of steel products today contain recycled material, just like aluminium. The use of electric arc furnaces has further reduced steel manufacturing’s environmental footprint.
History and Production
Aluminium:
- Originated in ancient times but was refined for industrial use in the 19th century.
- Produced from bauxite ore, which undergoes the Bayer process to become aluminium oxide, eventually reduced to the metal.
Steel:
- Has been in use for millennia, with ancient civilizations using varying forms.
- Produced from iron ore, primarily through the blast furnace route, then alloyed with carbon.
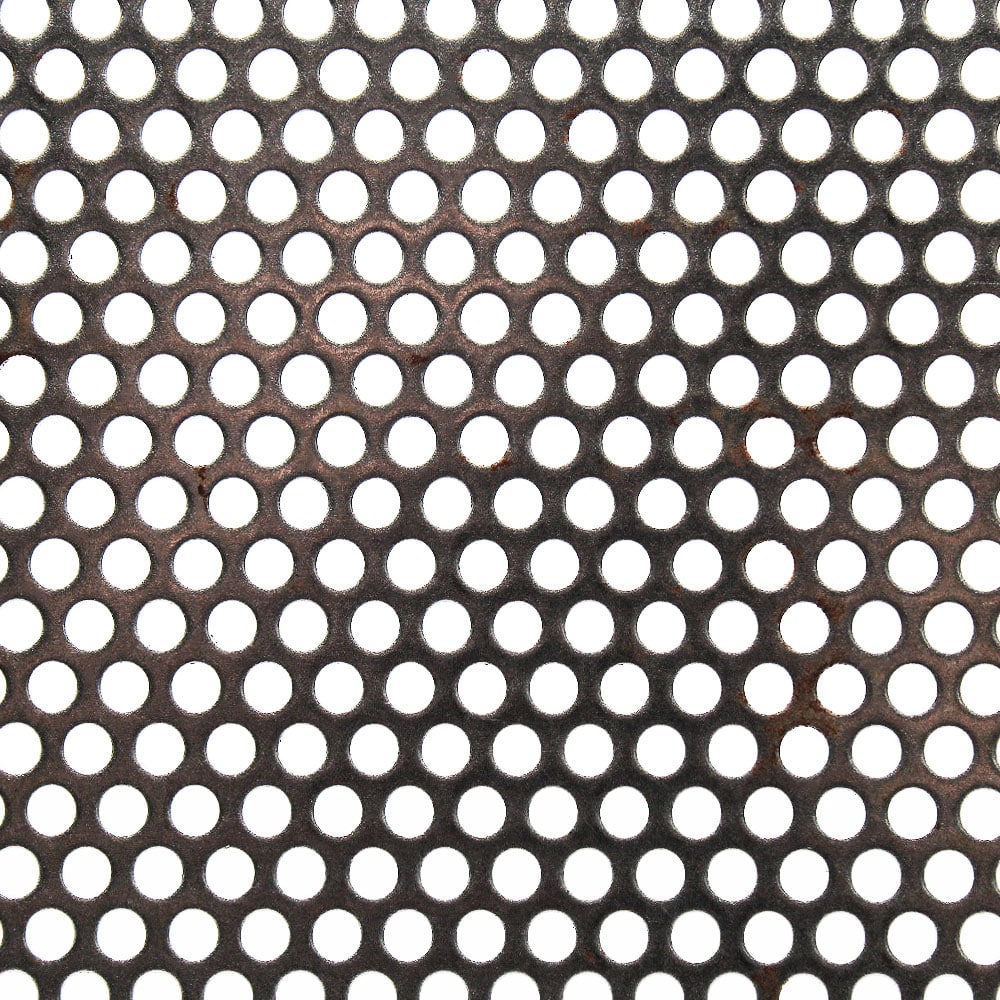
Physical Properties
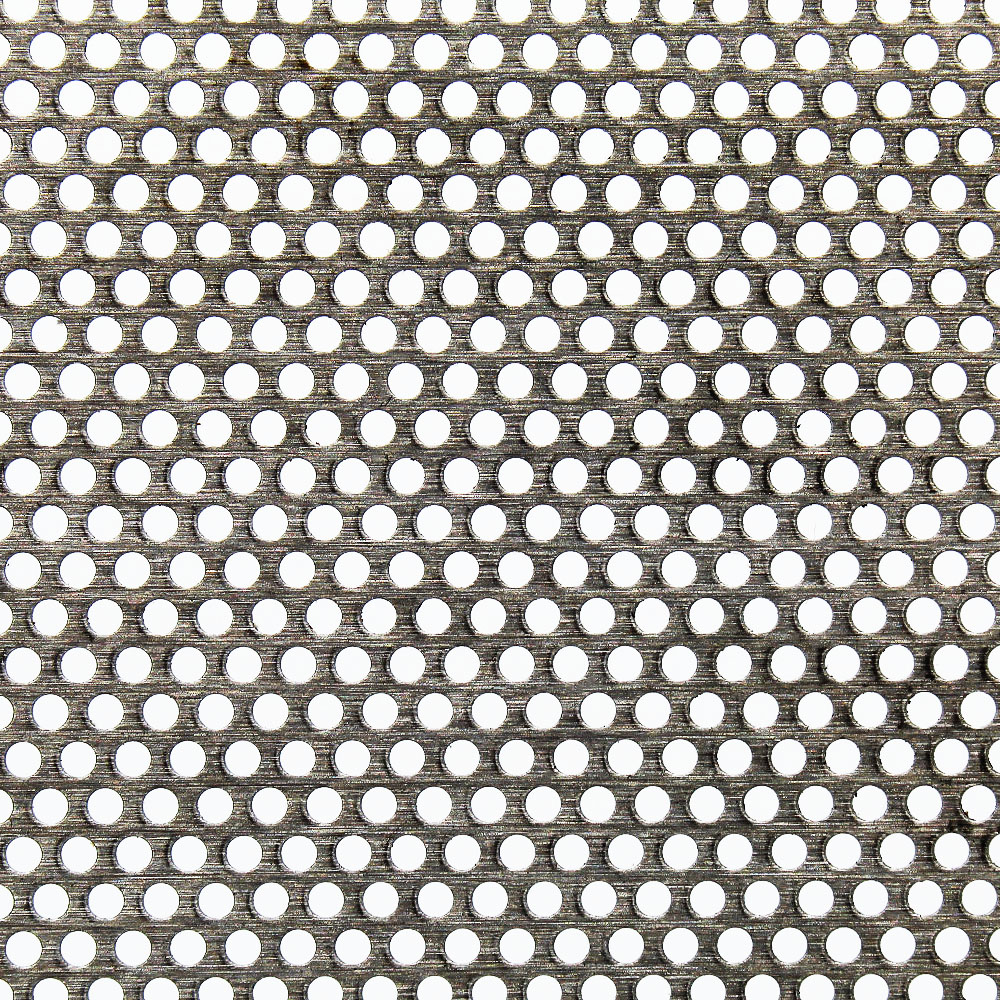
Aluminium:
- Lightweight, making it ideal for applications requiring ease of transport and installation.
- Non-magnetic nature ensures it doesn’t interfere with electronic devices.
Steel:
- Denser and heavier than aluminium, granting it higher tensile strength.
- Magnetic property can be useful for specific applications but can be a hindrance around sensitive electronics.
Corrosion Resistance
Aluminium:
- Naturally forms a protective oxide layer when exposed to air, rendering it highly resistant to corrosion.
- Ideal for outdoor applications, especially in more corrosive environments like coastal regions.
Steel:
- Unless treated or stainless, it’s more susceptible to rust.
- Stainless steel variants offer excellent corrosion resistance, albeit at a higher cost.
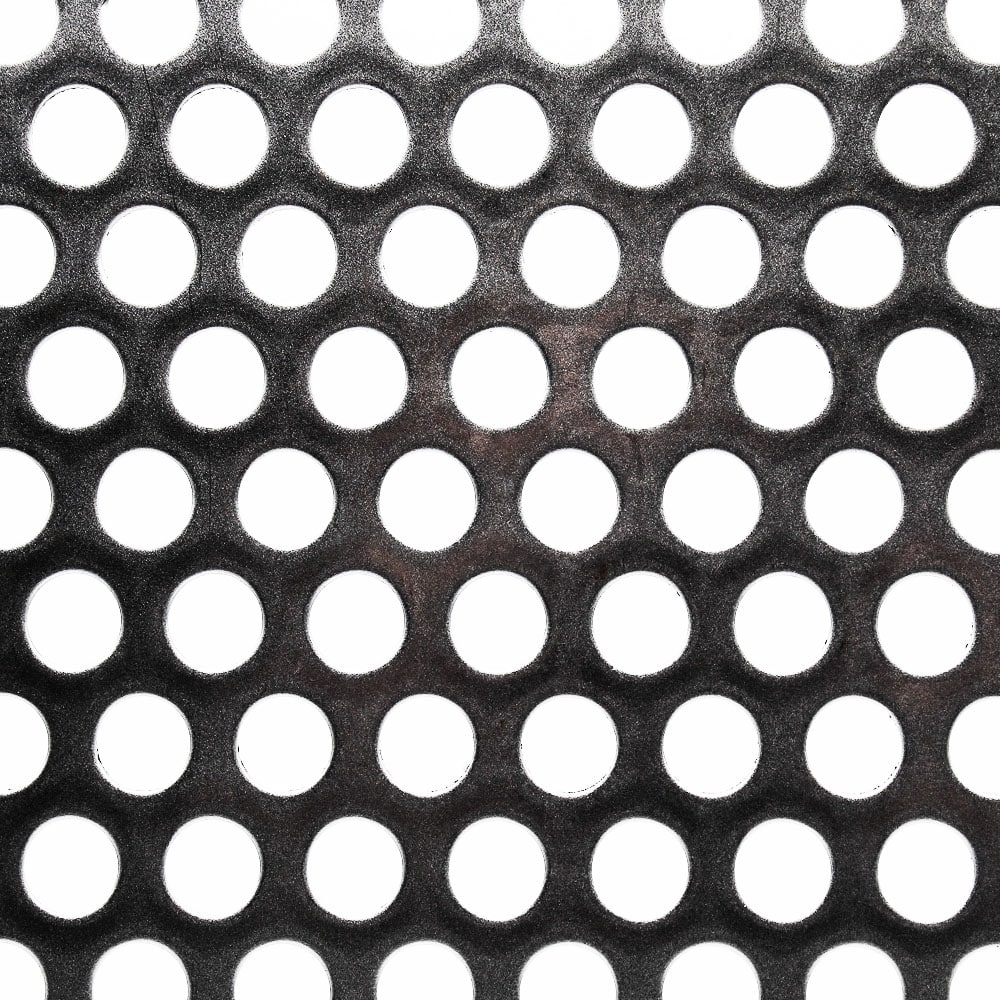
Flexibility and Formability
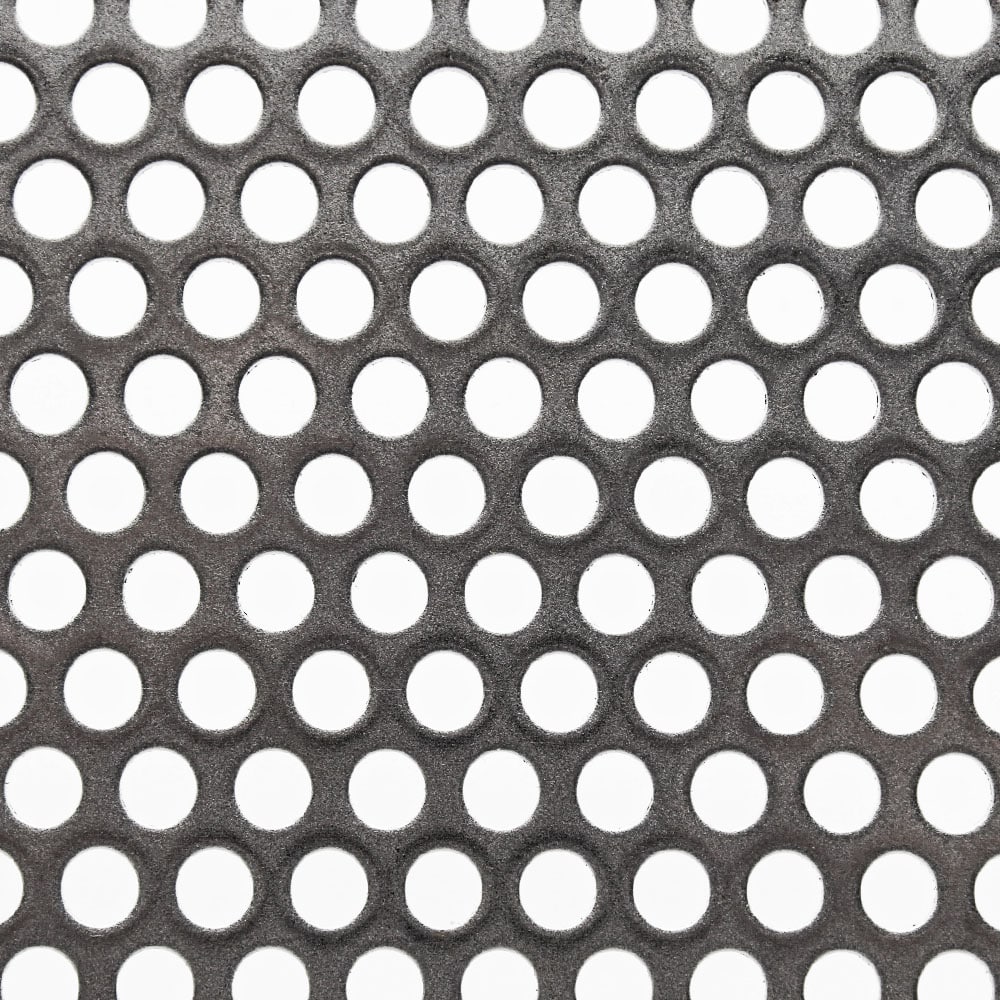
Aluminium:
- Known for its malleability, allowing it to be easily shaped without breaking or cracking.
- Excellent for intricate designs and patterns in perforated screens.
Steel:
- While flexible, it’s generally less malleable than aluminium.
- Suitable for applications requiring robustness and rigidity.
Aesthetic Appeal
Aluminium:
- Provides a sleek, modern look.
- Can be anodized to provide a range of colors, enhancing design possibilities.
Steel:
- Offers a classic, industrial aesthetic.
- Can be painted or coated for added visual appeal.
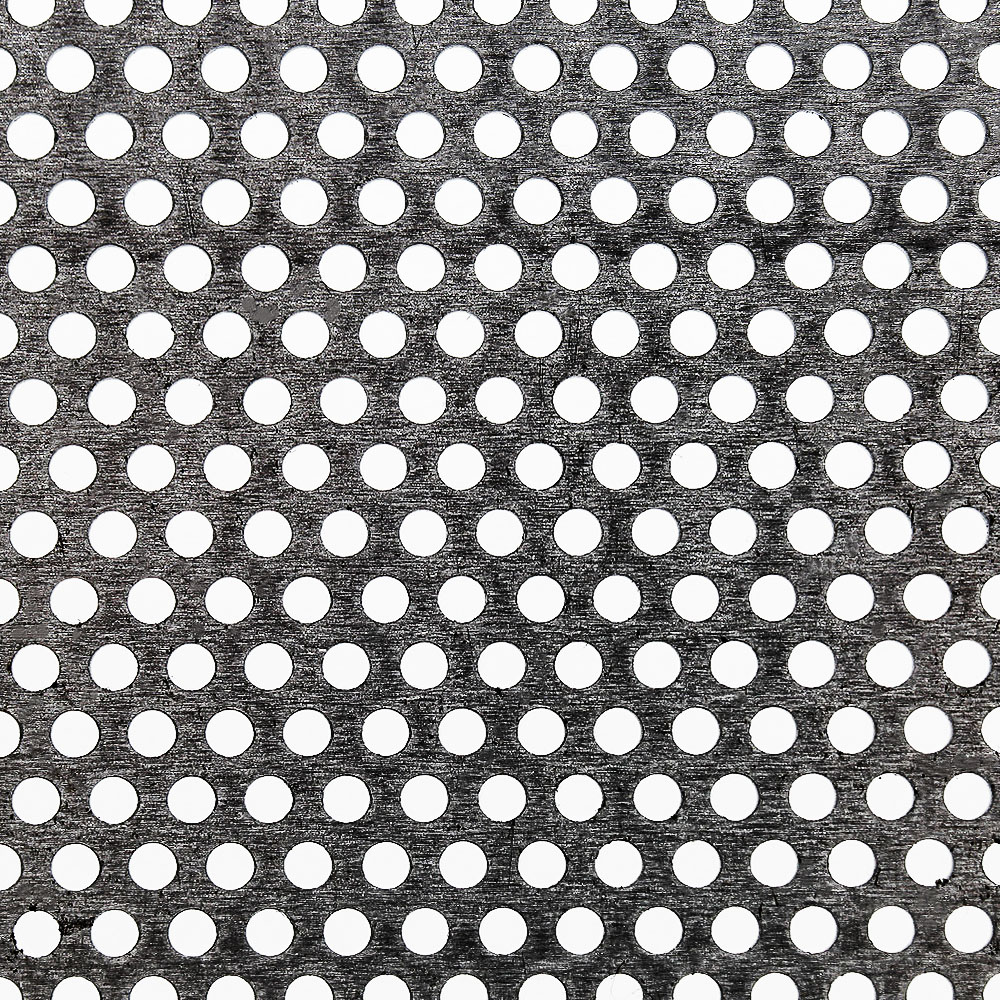
Cost Implications
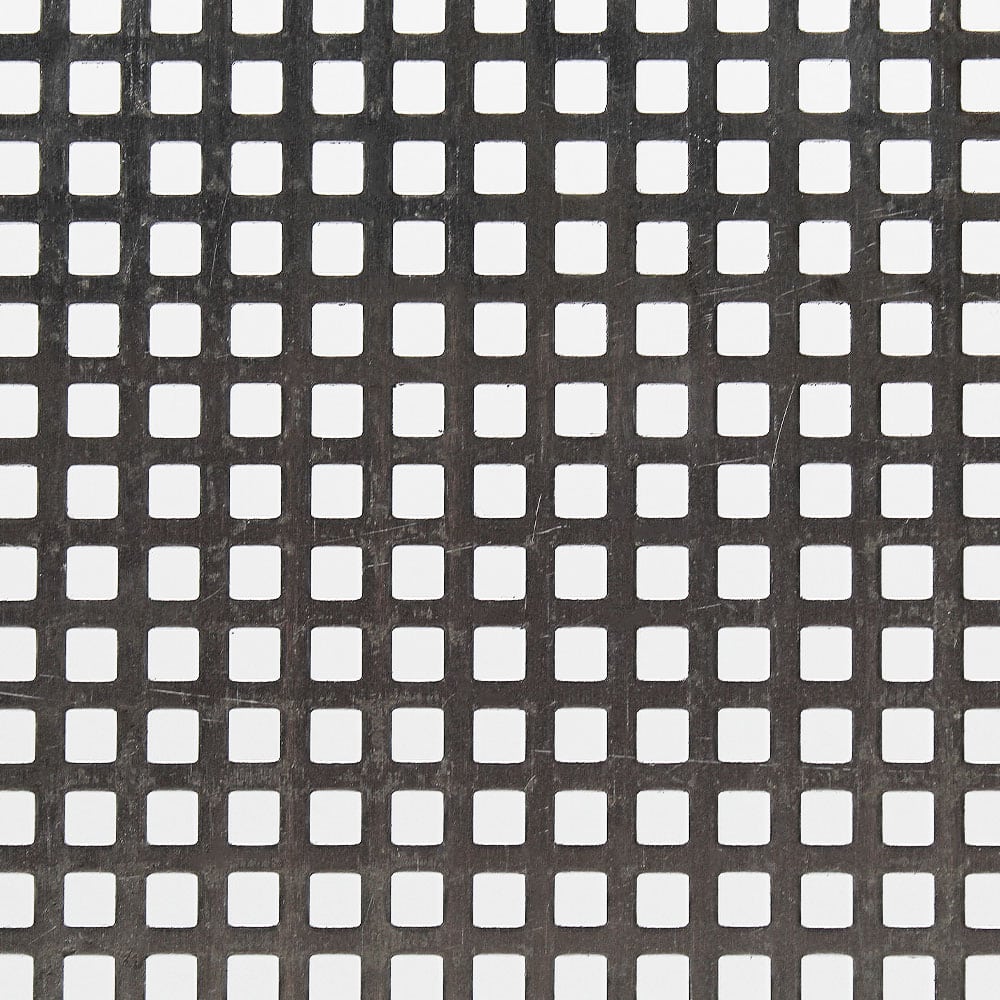
Aluminium:
- Generally more expensive than regular steel, though competitive with certain stainless steel grades.
- Longevity and low maintenance can offset the initial investment.
Steel:
- A wide range of grades and prices are available, with stainless steel being on the higher end.
- Regular maintenance, especially for non-stainless variants, might increase long-term costs.
Environmental Impact
Aluminium:
- Highly recyclable, with a significant portion of aluminium products being made from recycled material.
- Production is energy-intensive, but its longevity and recyclability can mitigate the environmental footprint.
Steel:
- Also recyclable, with many steel products containing recycled content.
- Steel production, particularly from virgin materials, has a substantial carbon footprint.
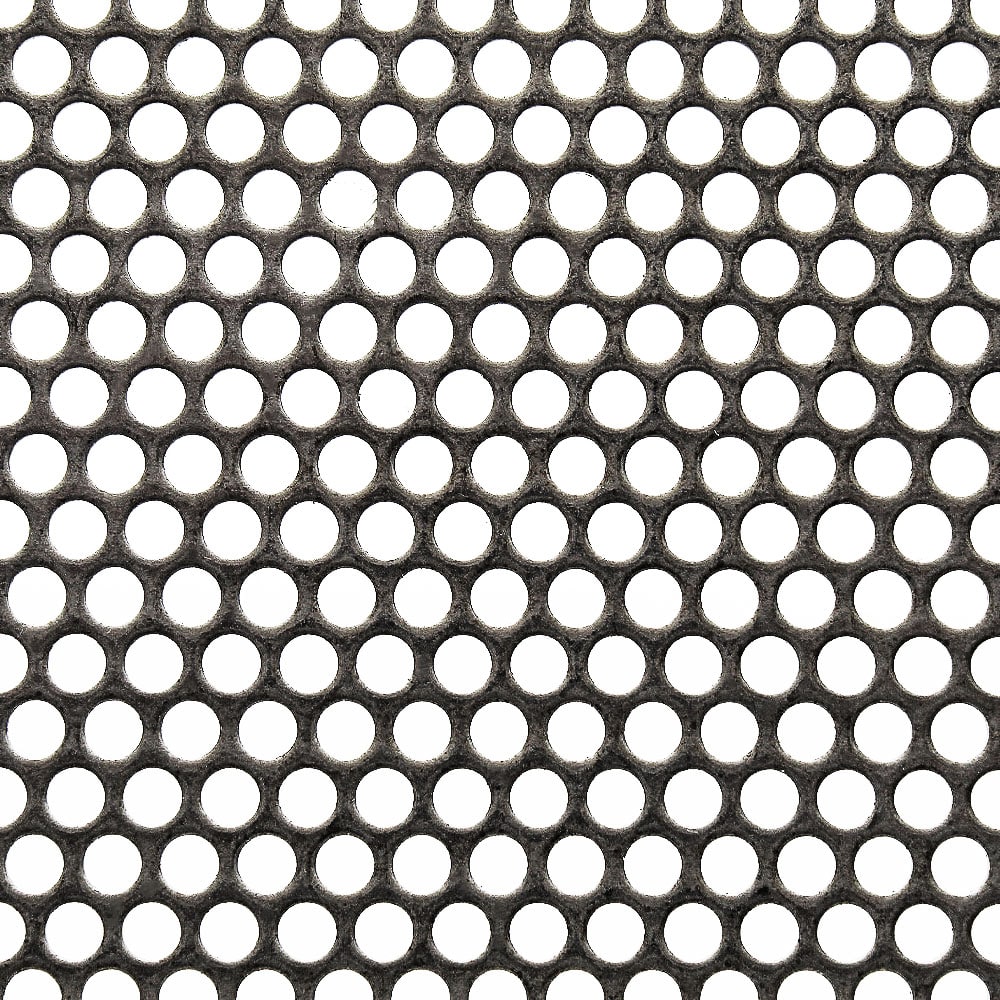
Applications
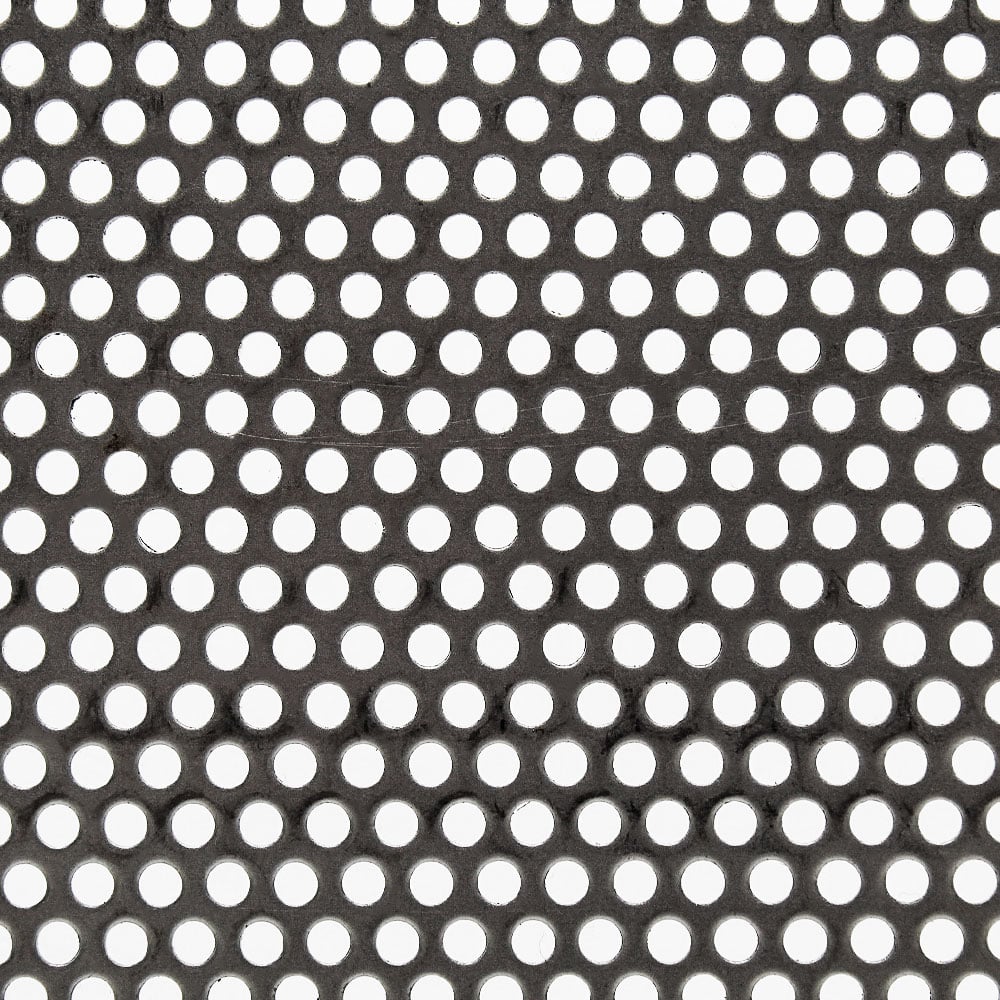
Aluminium:
- Popular for architectural facades, decorative panels, and electronics enclosures.
- Widely used in transportation due to its lightweight nature.
Steel:
- Commonly found in industrial settings, barriers, and security screens.
- Favoured for its robustness in heavy-duty applications.
When weighing up the above our conclusion is:
The versatility of aluminium makes it a better choice for a wider range of applications. Due to its lightweight nature, inherent strength, corrosion resistance, anodising capabilities, and environmental benefits, it is an ideal choice for many modern settings, particularly architectural and design-forward ones.
In contrast, steel is a stalwart in environments that require sheer resilience and robustness. For heavy-duty applications and settings where maximum strength is a priority, its tensile strength and durability make it an ideal choice.
In conclusion, while aluminium offers a diverse range of advantages making it suitable for various modern applications, the choice between aluminium and plain steel ultimately hinges on the specific requirements and priorities of the project at hand.
We cannot pick a winner.
As always, thank you for checking out our blog. We hope that this helps you with your project. We try to launch a couple of new guides every week. Eventually we will have covered everything there is to cover about mesh.
Keep an eye out for more articles in our ‘vs’ series.
You may be interested in our blog that discusses everything that you need to know about stainless steel perforated mesh.
Our goal for our blogs and help guides is to answer as many questions as possible to help to explain the possibilities of mesh to our customers.
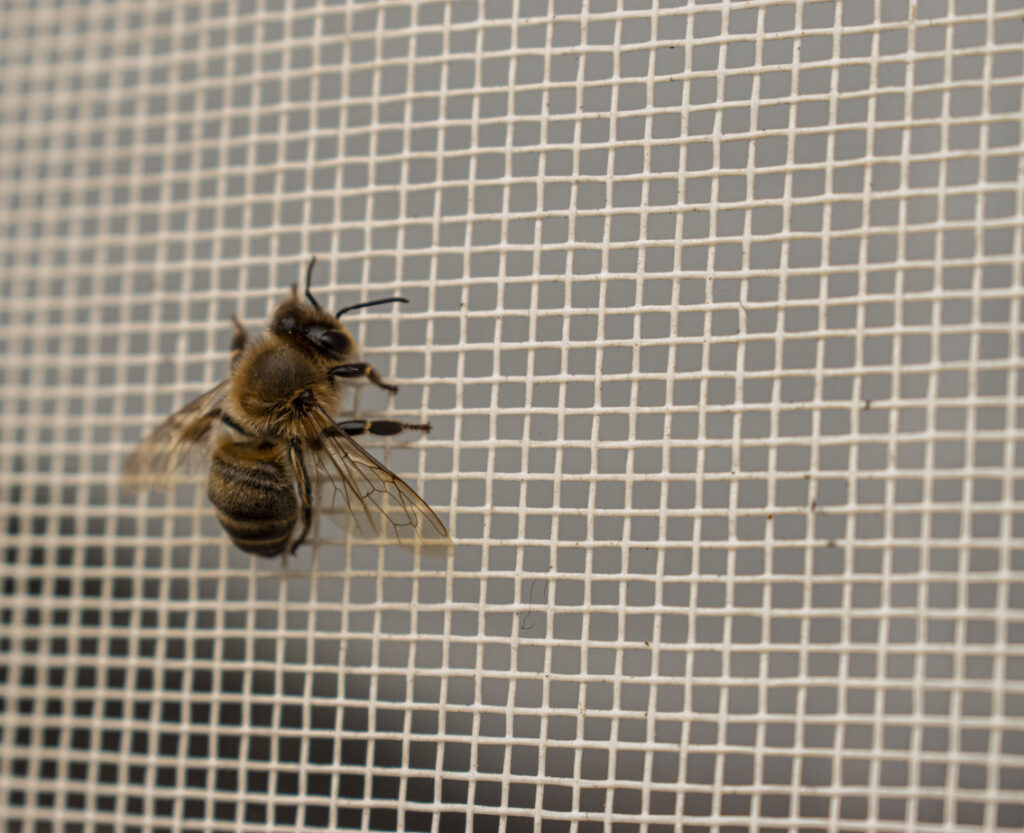
Hive Mesh for Beekeeping: Safer Hives with Stainless Steel Mesh
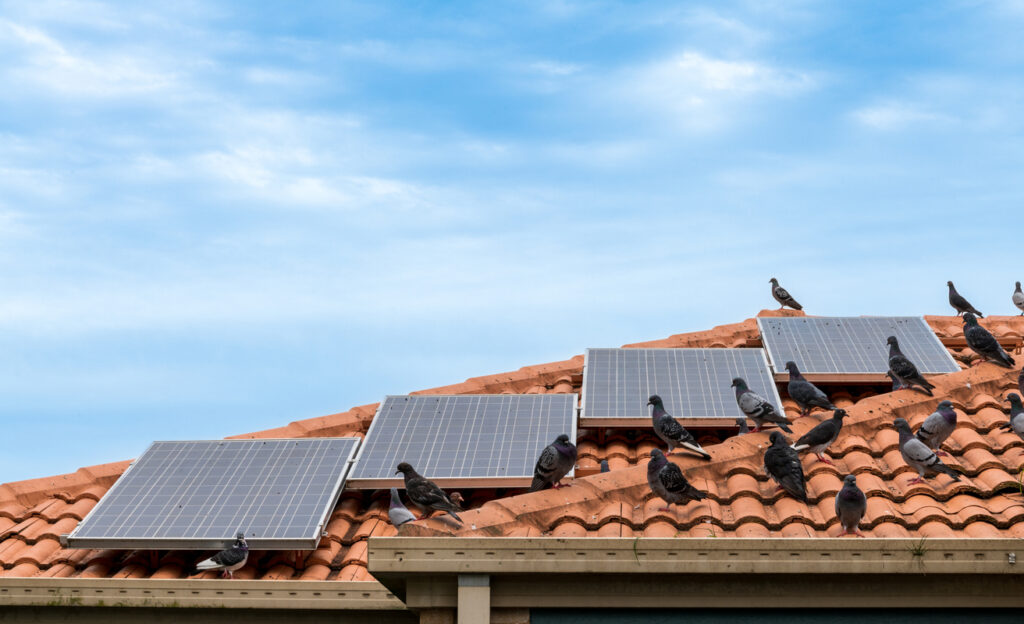
How To Use Solar Panel Mesh to Stop Birds Nesting Underneath
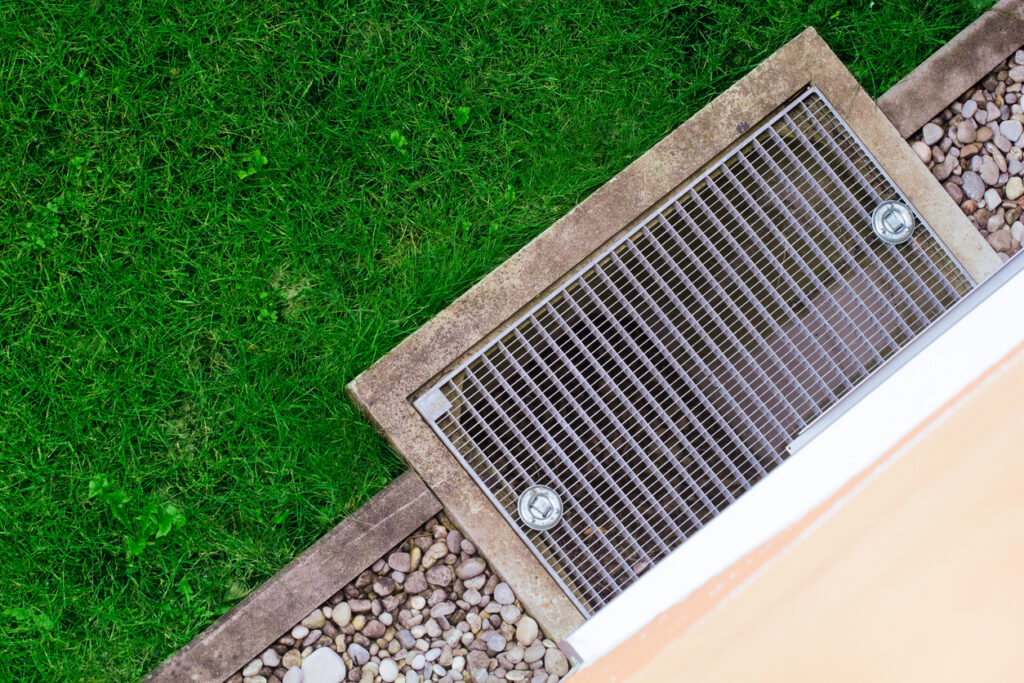
Choose the right stainless steel mesh for outdoor drainage.
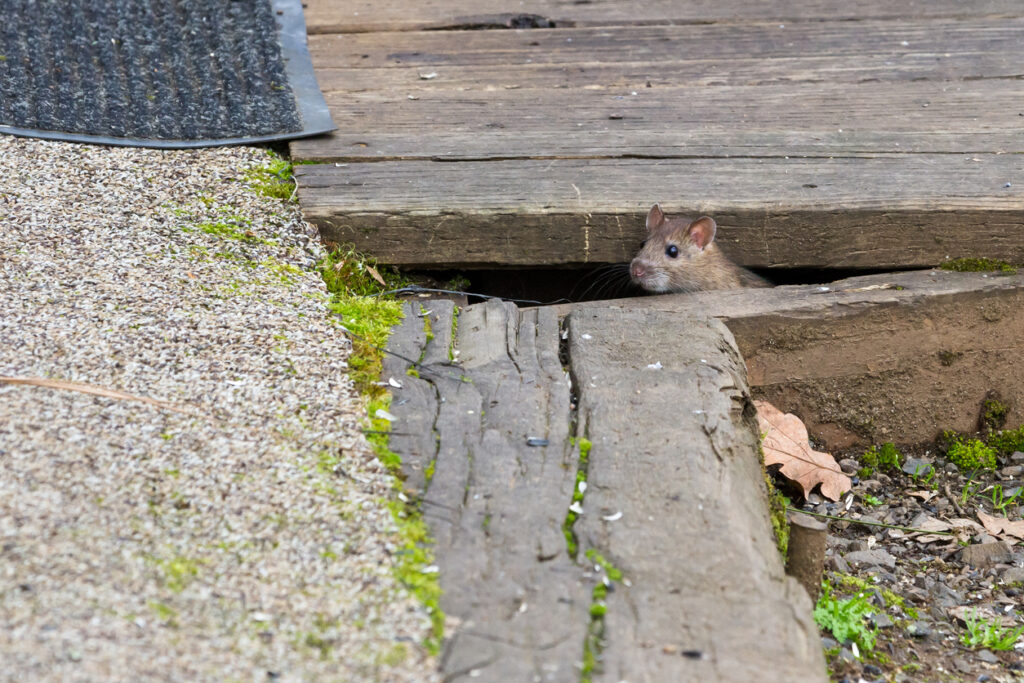
Installing Pest Proof Mesh Under Decking to Keep Pests Out
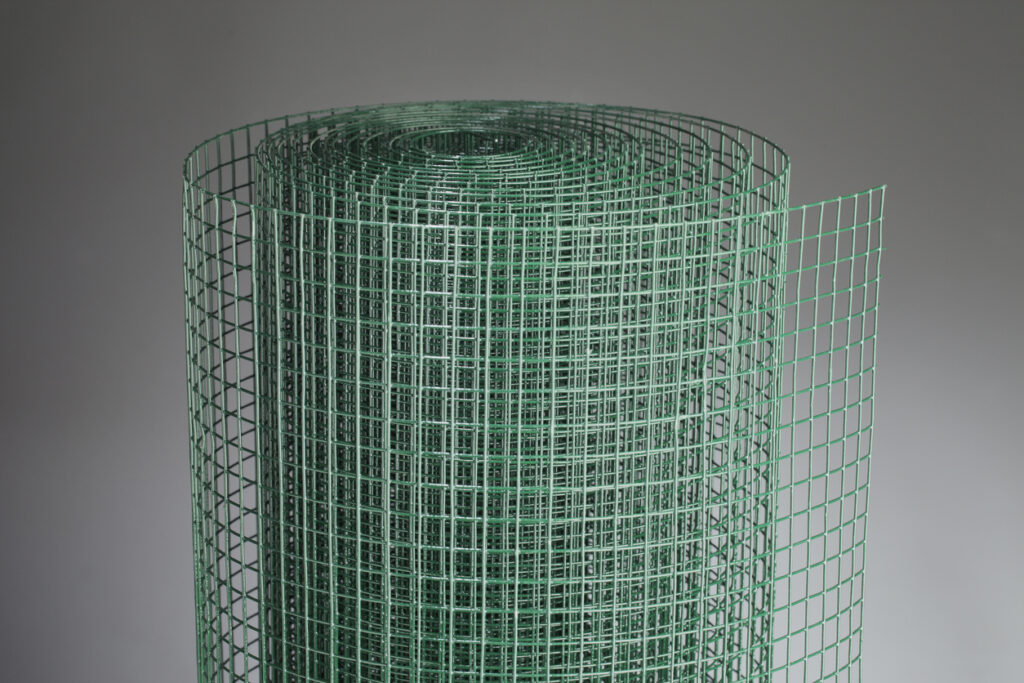
How Different Metal Coatings Affect Mesh Performance
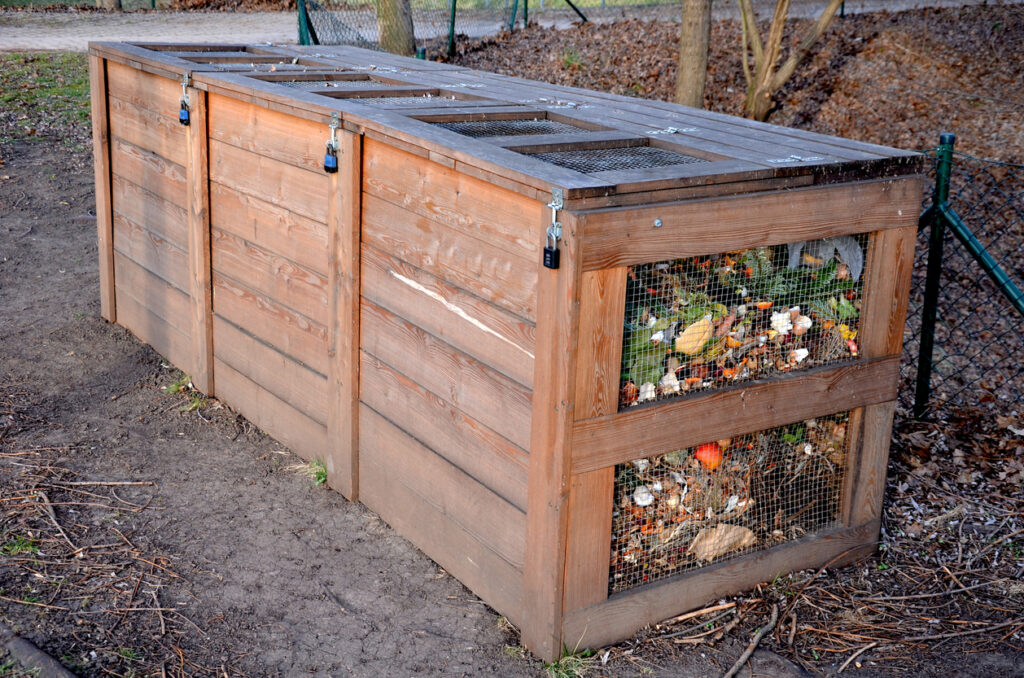
Creating a Pest-Proof Compost Bin with Metal Mesh
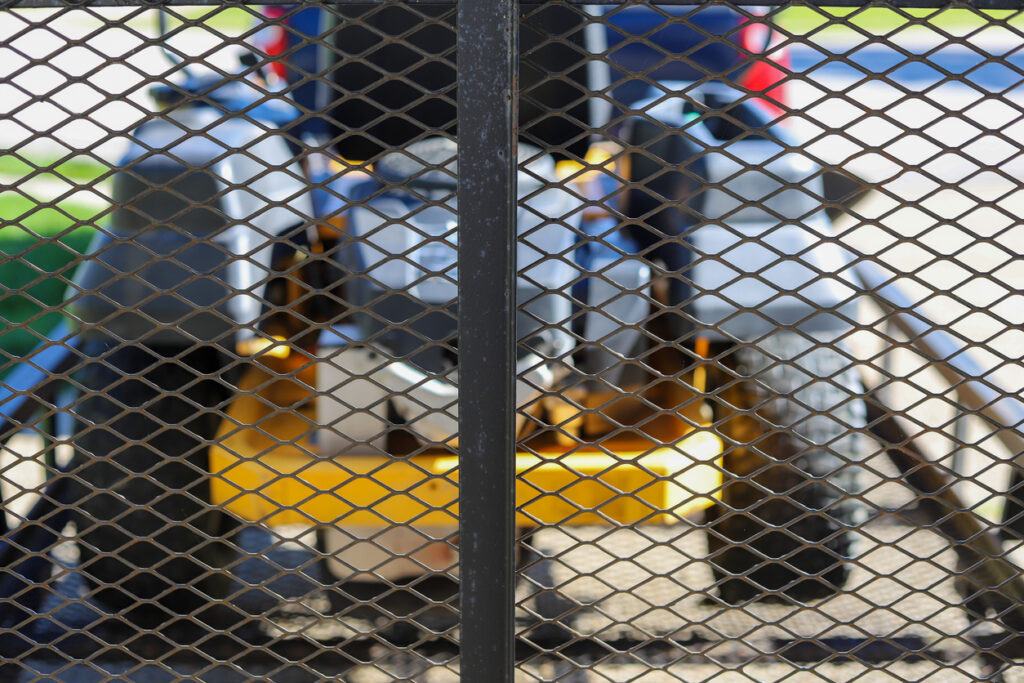
Why Wire Mesh Machine Guards Are Ideal for Safety Screens
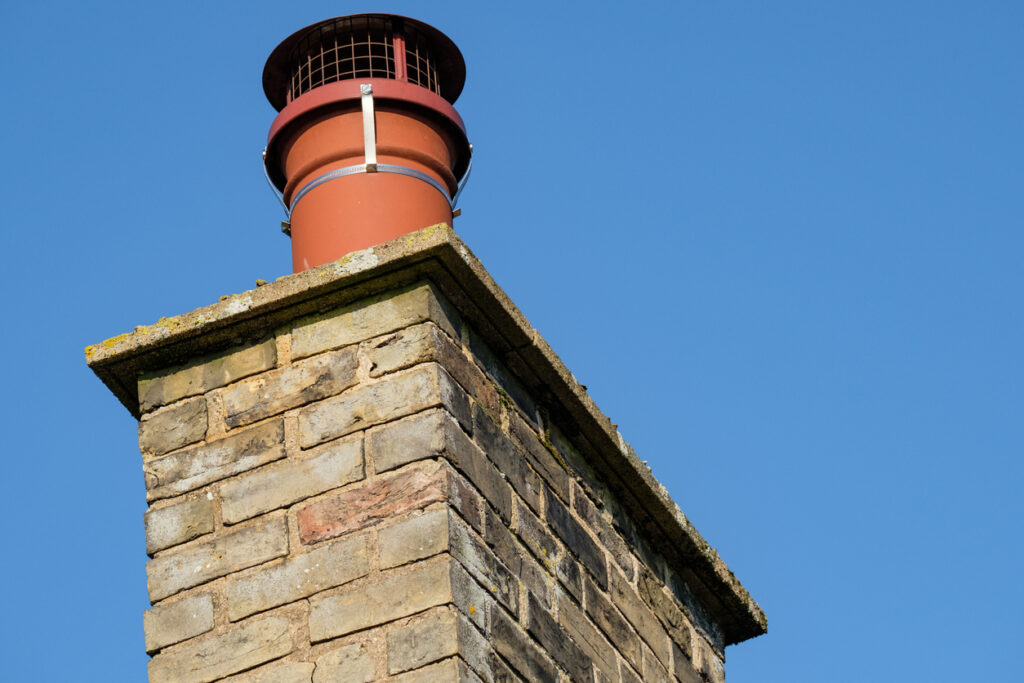
Choosing the Right Mesh for Chimney and Vent Protection
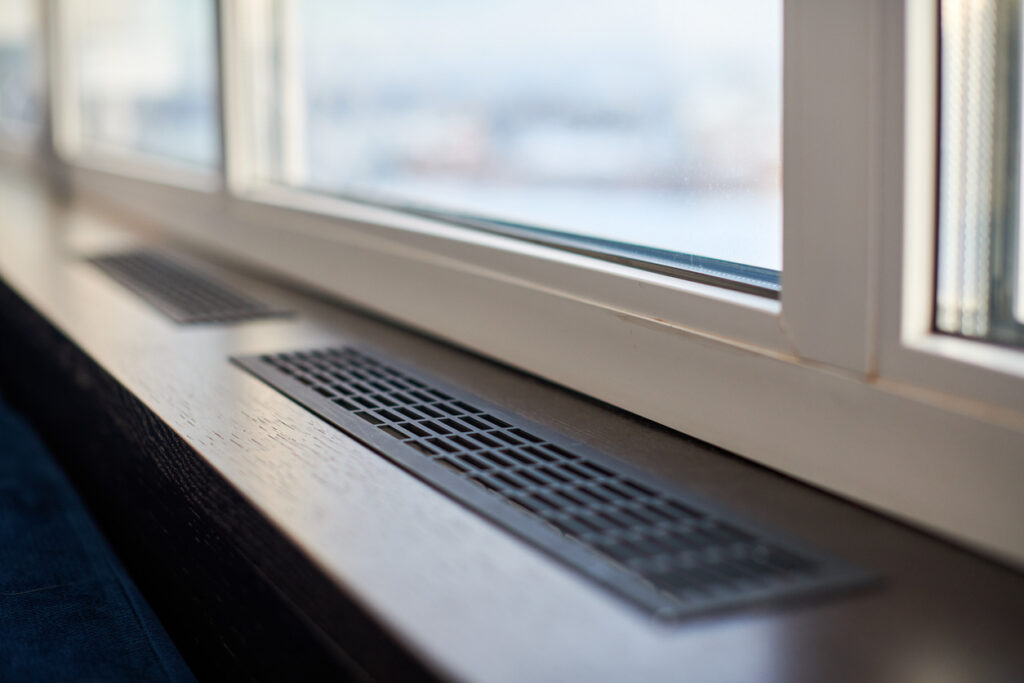